Thermopaket für emaillierte Reaktoren
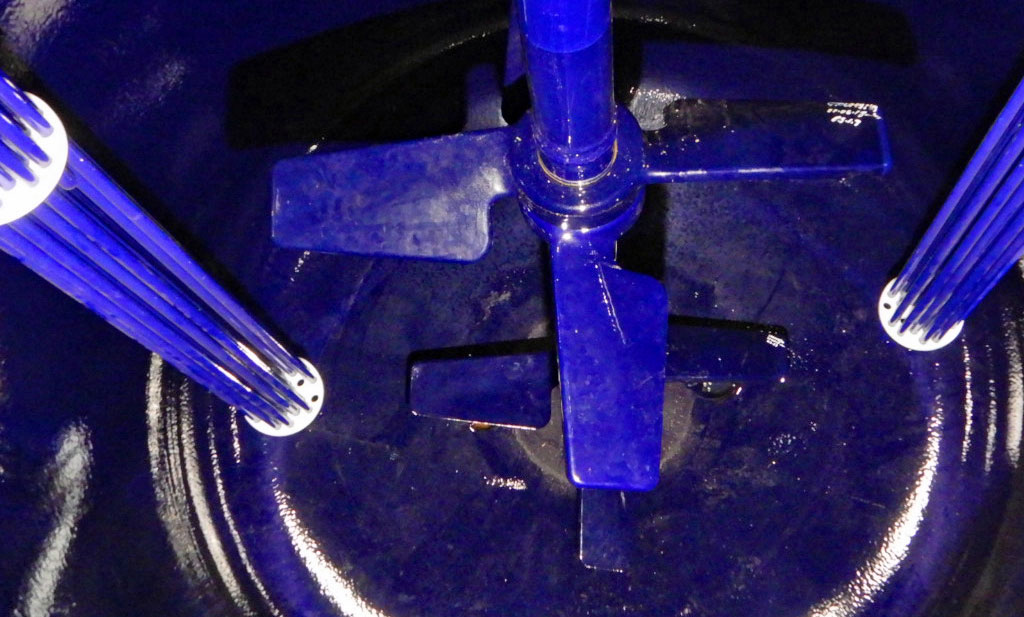
Einführung
An emaillierte Reaktoren wird eine Vielzahl an Anforderungen gestellt, um chemische Reaktionen unter aggressiven Bedingungen sicher zu betreiben. Diese umfassen bspw. die hohe korrosive Beständigkeit, sehr gute Reinigbarkeit, der Betrieb als Druckgerät, Vermeidung elektrostatischer Aufladungen, eine hohe Produktivität bei verschiedensten Prozessen oder ein adäquater Wärmetransport. Insbesondere der letzte Punkt rückt immer mehr in den Fokus, sodass ein energieeffizienter Betrieb gefordert wird. Steigende Energiepreise sowie politische Richtlinien und Verordnungen halten berechtigterweise Unternehmen zur Übernahme einer gesellschaftlichen ökologischen Verantwortung an. Ein energieeffizienter Betrieb umfasst dabei im Wesentlichen die Themenkomplexe der Wärmezufuhr oder -abfuhr und die Energiebereitstellung für den Rührerantrieb. Dieser Artikel gibt einen Überblick über die Möglichkeiten zur Wärmeübertragung in emaillierten Reaktoren und fasst kurz die Vor- und Nachteile der verschiedenen Optionen zusammen. Schwerpunkte sind Themen wie Doppelmantel vs. Halbrohrschlange, die Isolierung eines Reaktors, Einflussgrößen auf den Wärmdurchgang und die Bereitstellung zusätzlicher Wärmeaustauschfläche.
Doppelmantel vs. Halbrohrschlange
Ein oft kontrovers diskutiertes Thema ist der Einsatz einer Halbrohrschlange oder eines Doppelmantels. Beide Varianten weisen Vor- und Nachteile unter bestimmten Einsatzbedingungen auf. Folgende Tabelle gibt einen generellen Überblick über verschiedene Aspekte im direkten Vergleich.
Doppelmantel
+
- Ausnutzung der kompletten Wärmeaustauschfläche
- kostengünstigere Fertigung
- geringerer Druckverlust
- turbulente Spiralströmung durch Strömungsdüsen
- einfache Tragkonstruktion
- günstiger Kondensatabfluss bei Dampf
- einfache Reparatur des Innenkessels bei Schäden oder Durchbrüchen
- Reemaillierung bis 3 mal problemlos möglich
- einfache Aufarbeitung des Mantelraumes (vollständige Zugänglichkeit nach Abtrennen des Doppelmantels)
Halbrohrschlange
+
- geringerer Volumenstrom
- einfache Fertigung mehrerer Zonen
- definierte Strömung
- höhere Drücke als 6 bar einfach realisierbar
- geringerer Verrohrungsaufwand
- Reemaillierung bis 2 mal problemlos möglich
- Mehrgängigkeit (Trennung von Servicekreisläufen)
-
- geringere Wärmeaustauschfläche (insbesondere bei mehrgängiger Ausführung)
- kostenintensivere Fertigung
- höherer Druckverlust
- aufwendigere Tragkonstruktion, um Verlust von Wärmeaustauschfläche zu vermeiden
- ungünstiger Kondensatabfluss bei Dampf
- risikobehaftete Reparatur des Innenkessels bei Schäden (Zustand der Schweißnaht?)
- schlechte bis keine Aufarbeitung des Innenraums einer HRS (keine Zugänglichkeit; lediglich Spülen)
- thermisch induzierte Wechselspannungsrisse (insbesondere am Boden)
Aus der Gegenüberstellung geht hervor, dass die Vorteile des Doppelmantels überwiegen. Nichtsdestotrotz ist der Einsatz einer Halbrohrschlange gerechtfertigt, wenn geringere Volumenströme, mehrere Kühl-/Heizzonen, die Trennung zwischen Kühl- und Heizmedium (Mehrgängigkeit) oder höhere Dampfdrücke (> 6 bar) gefordert werden. Ebenso ist der Verrohrungsaufwand in der Regel geringer.
Einflussgrößen auf den Wärmedurchgang
Emaille ist ein schlechter Wärmeleiter, sodass dessen Schichtstärke einen großen Einfluss auf den Wärmestrom (Q) hat und diesen begrenzt. Umso wichtiger ist die richtige Einstellung der weiteren Einflussparameter auf den Wärmedurchgang. Klassischerweise werden emaillierte Rührwerksapparate über einen Doppelmantel oder einer Halbrohrschlange temperiert. Die Wärmeaustauschfläche ist somit durch die Baugröße des Reaktors vorgegeben und begrenzt (A). Die Temperaturdifferenz (Δtm,log) zwischen Produkt und Servicemedium beeinflusst den resultieren Wärmestrom maßgeblich, sollte jedoch auf einem geringen Temperaturniveau gehalten werden, um die Wärmeverluste an die Umgebung zu minimieren.
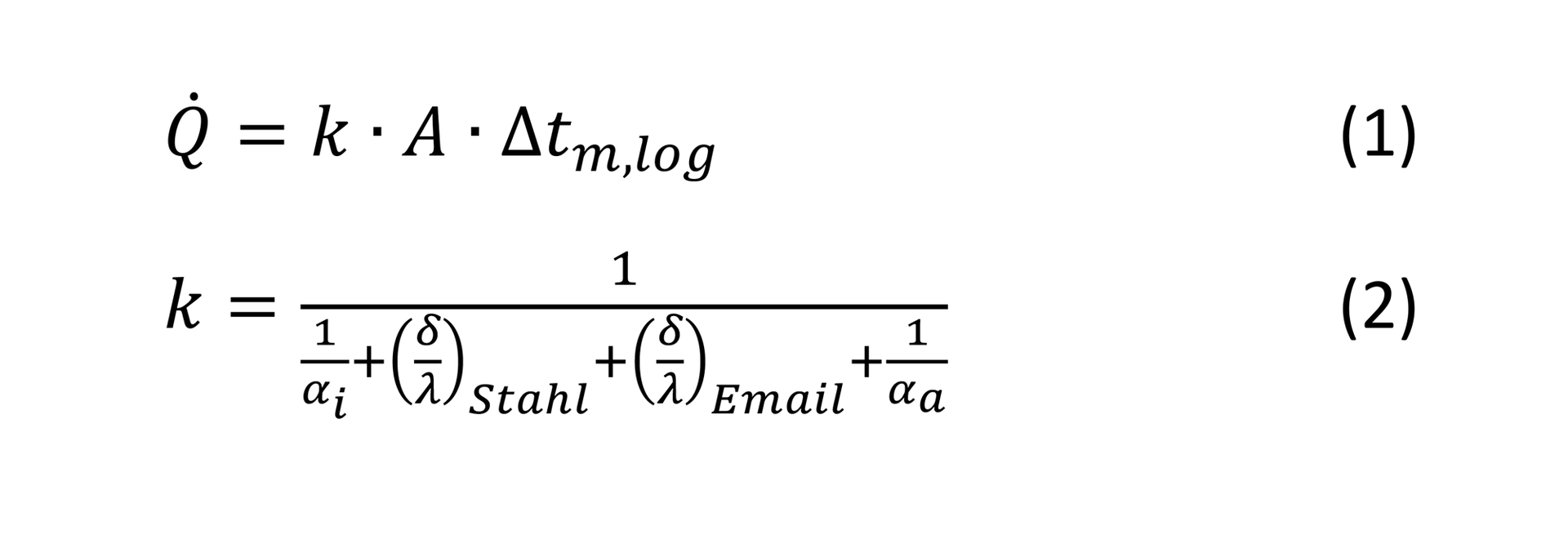
Zur Steigerung des Wärmedurchgangskoeffizienten (k) bestehen mehrere Möglichkeiten bei gegebener Wärmeleitung durch den Verbundwerkstoff Stahl/Emaille. Der Wärmeübergang (αa) zwischen der Außenwand des Innenkessels und dem Serviceraum des Doppelmantels/der Halbrohrschlange wird durch die Stoffparameter des Servicemediums sowie der vorherrschenden Strömungsgeschwindigkeit beeinflusst. Um einen günstigen Wärmeübergang zu erzeugen, sollte das Servicemedium folgende Stoffeigenschaften aufweisen:
- Hohe Wärmeleitfähigkeit
- Niedrige Viskosität
- Hohe Dichte
- Hohe spezifische Wärmekapazität
Eine hohe Strömungsgeschwindigkeit, bedingt durch den anliegenden Volumenstrom, erhöht ebenso den Wärmeübergang (αa). Diese Einflussgröße ist jedoch begrenzt und folgt einer Wurzelfunktion und nähert sich somit einem Grenzwert (Abbildung 2). Folglich erhöht eine Volumenstromsteigerung den übertragbaren Wärmestrom ab einem gewissen Bereich nur noch geringfügig und ist nicht sinnvoll.
Der Wärmeübergang (αi) an der Innenwand des Innenkessels und dem Produkt ist ebenfalls abhängig von den Stoffeigenschaften und den vorherrschenden Strömungsgeschwindigkeiten. Die stofflichen Einflussgrößen sind vom chemischen Prozess vorgegeben und können nicht geändert werden. Die Strömungsgeschwindigkeit im Produktraum wird von der Turbinenart und -anzahl sowie der Drehzahl bestimmt. Die Konfiguration der Turbine(n) und die Drehzahl können unter Umständen prozessbedingt nicht beliebig gesteigert werden (z. B. Kristallisation, Polymerisation). Ebenso folgt der Einfluss der Strömungsgeschwindigkeit wieder einer Wurzelfunktion und ist somit begrenzt. Darüber hinaus induziert die mechanische Leistung des Rührwerks einen Wärmestrom, welcher bei einem Kühlprozess kontraproduktiv ist (Abbildung 3).
Isolationsmaterialien für emaillierte Reaktoren
Eine Reduktion der Wärmeverluste an die Umgebung und folglich die Steigerung der Energieeffizienz kann mit einem Isoliermantel erfolgen. Dieser kann den zylindrischen Teil und den unteren Boden oder den kompletten Reaktor inklusive des aufwendig zu isolierenden oberen Bodens umfassen. Typische Isolationsmaterialien sind Foamglas, Mineralwolle oder Steinwolle. Alle Materialien sind nicht brennbar und weisen unterschiedliche Wärmeleitfähigkeiten auf. Die Isolierdicke ist materialabhängig, wobei Foamglas nicht zur Isolierung des oberen Boden verwendet werden kann. Essentiell ist die Ummantelung mit dicht verschweißten Edelstahlblechen zur Vermeidung einer Korrosion des Reaktors im Isolierraum.
Das PowerBaffle - mehr Leistung und kürzere Prozesszeiten
Die gegebene Wärmeaustauschfläche ist durch die Baugröße des Reaktors (Doppelmantel oder Halbrohrschlange) vorgegeben und begrenzt. Sollen Kühl- oder Heizprozesse schneller oder mit größerer Sicherheit erfolgen, ist die übertragbare Wärmeleistung zu erhöhen. Eine deutliche Steigerung der Wärmeleistung kann über die Vergrößerung der Wärmeaustauschfläche erfolgen. Emaillierte Rohrbündelwärmetauscher – PowerBaffle K014 – stellen dabei ein einzigartiges System zur signifikanten Steigerung der Wärmeaustauschfläche dar. Diese erhöhen nicht nur deutlich die Wärmeaustauschfläche und damit die Wärmeleistung, sondern stellen diese auch mit geringen Betriebskosten zur Verfügung! PowerBaffle weisen in Abhängigkeit der Randbedingungen einen 2,5- bis 3-mal höheren Wärmedurchgangskoeffizienten gegenüber einen emaillierten Behälter auf. Daher stellt die Oberfläche eines PowerBaffle hinsichtlich der Wärmetechnik eine besonders hochwertige Wärmeaustauschfläche dar! Dies liegt in der angewendeten Emaillierungstechnik mit Hilfe des PUESTA-Verfahrens (Pulver-Elektrostatisches-Verfahren) begründet. Eine gleiche Korrosionsbeständigkeit gegenüber der Standardemaillierung (Kessel, Turbinen, Stromstörer) wird erreicht – jedoch genügt eine kleinere Schichtdicke der Emaillierung und somit ist der Wärmedurchgang gesteigert. Ein oder mehrere PowerBaffle können parallel oder seriell zum Doppelmantel/Halbrohrschlange geschalten werden. Die Parallelschaltung könnte auch zur Trennung der Heiz- und Kühlkreisläufe genutzt werden
Zusammenfassung
Die aufgeführten Aspekte verdeutlichen, dass hinsichtlich der Wärmetechnik verschiedene Grenzen und Einflussgrößen zu berücksichtigen sind. Zudem geht hervor, dass die Erhöhung der Wärmeaustauschfläche den ökologischsten und ökonomischsten Weg zur Steigerung des verfügbaren Wärmestroms darstellt. Hierfür bietet THALETEC weltweit als einziger Hersteller das PowerBaffle K014 an, welcher signifikant den Wärmestrom steigert und gleichzeitig als Stromstörer sowie Temperatursensor fungiert. Sprechen Sie uns einfach an, wenn Sie Fragen zur Wärmetechnik emaillierter Reaktoren haben. THALETEC bietet Ihnen die Beurteilung und Berechnung der verschiedenen wärmetechnischen Fragestellungen an process@thaletec.com.