55 % weniger CO2 durch Reemaillieren bei THALETEC
Durch Reemaillieren bei THALETEC statt dem Neubau eines emaillierten Rührwerksapparates lassen sich mehr als die Hälfte der CO2 Emissionen vermeiden.
Die Chemie- und Pharmaindustrie weisen allgemein einen hohen Energieaufwand nicht nur während des Betriebs ihrer Anlagen auf, sondern ebenso bei der Herstellung notwendiger Apparate, wie bspw. Wärmetauscher, Rührwerksapparate oder Dünnschichtverdampfer. Enorme Wärmeströme sowie Antriebsleistungen gilt es möglichst effizient zu übertragen und intelligent weiterzuverwenden. Ressourcenknappheit und -verteuerungen sowie der „Green Deal“ der EU [1] und nationale Verordnungen halten Unternehmen zu einer energieeffizienten Infrastruktur an, um eine gesellschaftliche Verantwortung zu übernehmen. Insbesondere die Chemie- und Energiebranche stellen durch ihren hohen Energieverbrauch eine entscheidende Stellschraube dar.
Emaillierte Rührwerksapparate – Herz vieler chemischer Verfahren
Emaillierte Rührwerksapparate sind ein Kernelement der Chemie- und Pharmaindustrie und weisen, bedingt durch den hohen Stahleinsatz und dem Emaillierprozess, einen entsprechenden Energieaufwand während der Herstellung auf. Aufgrund der häufigen Fertigung und der damit einhergehenden Datenbasis soll dies exemplarisch an dem genormten Rührwerksapparat CE – 16 000 – 2600 – AM (in Anlehnung an DIN 28136 3) mit Hilfe des THALETEC-spezifischen Energieaufwands für den Herstellprozess verdeutlicht werden (Abbildung 1). Dem gegenüber wird ein baugleicher reemaillierter Rührwerksapparat gestellt.
Ein emaillierter CE 16.000 Rührwerksapparat mit Außenmantel wiegt, vollausgestattet mit Rührwerk, Rührer und Stromstörer, etwa 17 Tonnen [2]. Etwa 10 Tonnen entfallen auf den so genannten „Innenkessel“, dem emaillierten Druckbehälter. Der Durchmesser des Appa¬rates beträgt 2.700 mm, die Länge des Behälters 4.080 mm. Steht der Behälter auf Rohrfüßen und besitzt er einen Antrieb, beträgt die Gesamthöhe etwa 7.100 mm. Der Apparat hat ein Nenn Fassungsvermögen von 16.000 und ein Gesamtvolumen von etwas über 18.000 l.
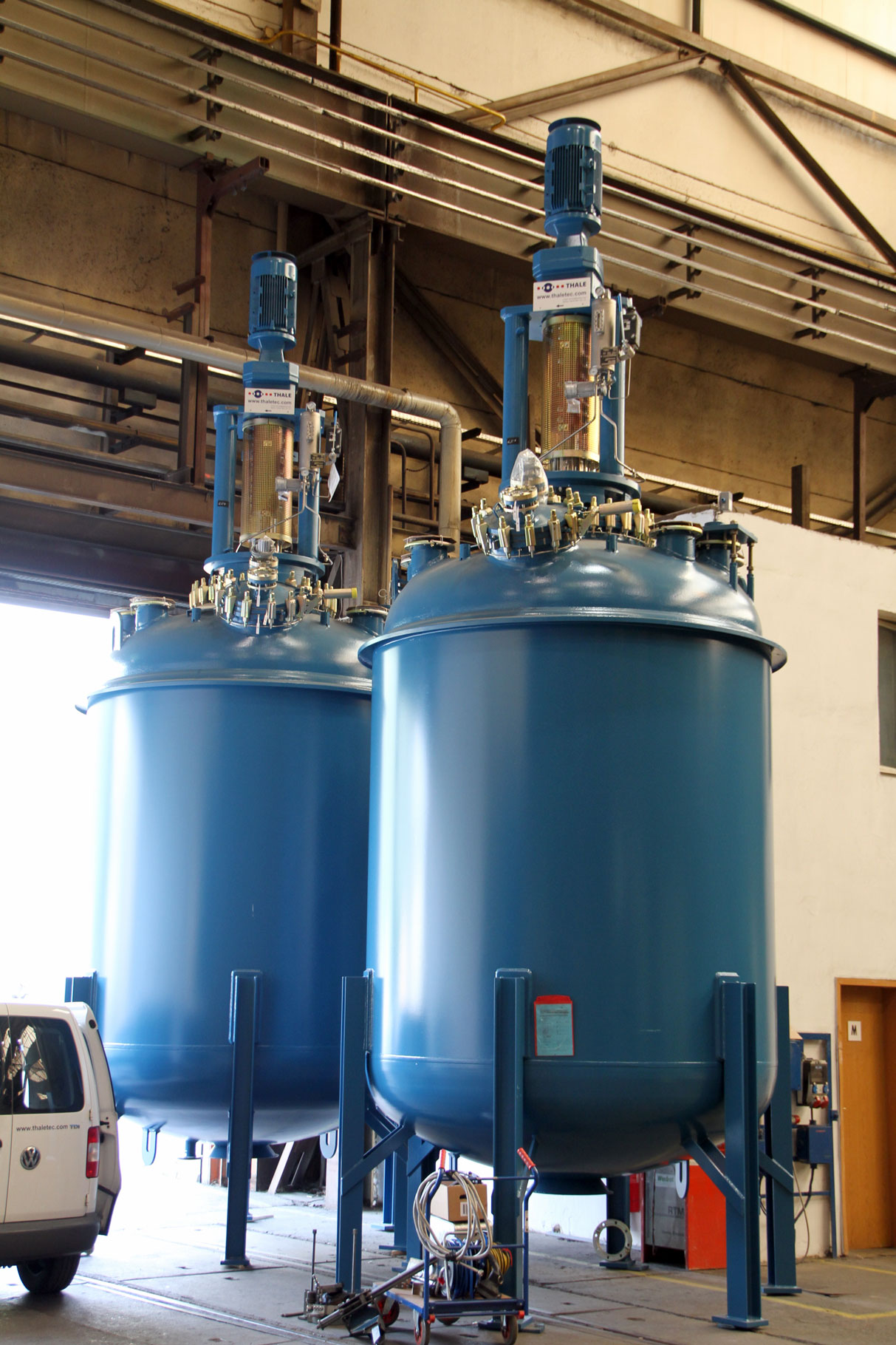
Abbildung 1: CE 16000 emaillierter Rührbehälter
Energetische Betrachtung
Bei den energetischen Betrachtungen werden die Aspekte der Stahlherstellung und der werksinternen Fertigung inklusive des Emaillierungsprozesses berücksichtigt. Laut einer Studie aus dem Jahr 2020 werden zur Herstellung einer Tonne Stahl ca. 3.962 kWh benötigt [3]. Dieser Wert beinhaltet sowohl den Primär- als auch Sekundärstahl. Dabei teilen sich die Primärerzeugung aus Eisenerz zum Sekundärstahl aus Schrott zu ca. 70 zu 30 % auf [3]. Bei einer Gesamtmasse eines CE16000 von rd. 17,95 t (inkl. Antrieb, Rührwerk, Stromstörer etc.) werden demzufolge zur Stahlherstellung ca. 71.100 kWh benötigt. Demgegenüber wird bei einer Reemaillierung der Stahl weitestgehend weiterverwendet. Werksinterne Berechnungen zeigen, dass der Energieaufwand für den Rohbau und die sonstigen Fertigungsschritte einer Neuanfertigung rd. 4.000 kWh und einer Reemaillierung ca. 2.200 kWh bedürfen.
Neben der Stahlerzeugung stellt der Emaillierprozess den zweiten energieintensiven Ferti-gungsprozess zur Herstellung eines emaillierten Rührwerksapparates dar. Dabei ist der Energieaufwand für das Emaillieren eines neu angefertigten Behälters und eines reemaillierten Behälters mit rd. 56.200 kWh gleichwertig. In Abbildung 2 sind die energetischen Anteile zur Herstellung eines Rührwerksapparates grafisch dargestellt.
Wiederverwendung des Stahlkörpers spart CO2
In Summe ist für eine Neuanfertigung des CE16000 ein energetischer Aufwand von rd. 131.300 kWh erforderlich. Dem gegenüber steht die Alternative einer Reemaillierung mit rd. 58.400 kWh. Dies entspricht einer Energieeinsparung von -55 %. Diese wird vorwiegend durch das Einsparen der Energie für die Stahlherstellung begründet.
Dieser gravierende Unterschied spiegelt sich ebenso im CO2-Footprint wider. Unter der Annahme des deutschen Strommixes im Jahr 2019 (0,408 kg/kWh) [4] werden für die Neuanfertigung eines CE16000 rd. 53,6 t und für die Reemaillierung rd. 23,8 t Kohlenstoffdioxid emittiert (Abbildung 3).
Gesellschaftliche Verantwortung übernehmen
Die THALETEC GmbH nimmt die gesellschaftliche Verantwortung wahr und identifiziert ein hohes Einsparpotenzial an Treibhausgasen unter Verwendung regenerativer Energie.
Da die Brennöfen elektrisch betrieben sind, wäre somit die Fertigung inklusive des Emaillierprozesses nahezu ohne Emissionen bei 100 %-iger Verwendung regenerativer Energien möglich.
Noch mehr CO2-Einsparung durch effizienteren Betrieb möglich
Die vorliegenden und konservativen Ergebnisse verdeutlichen zudem, dass es nicht nur ökonomischer sondern auch ökologischer ist, einen effizienten Rührwerksapparat (anstatt mehrerer und ineffiziente) zu betreiben, der hohe Wärmeströme und somit kurze Heiz- bzw. Kühlzeiten sowie eine hohe Produktivität erlaubt.
Naturgemäß ist der Wärmedurchgang aufgrund der Wärmeleiteigenschaften der Emaillierung bei emaillierten Rührwerksapparaten geringer. Eine deutliche Steigerung des Wärmestroms ist mit dem PowerBaffle erzielbar, der an jeden Standardstutzen DN 200 bis DN 400 adaptierbar ist (Abbildung 4). Dieser stellt die Heiz- bzw. Kühlleistung zudem unter geringeren Betriebskosten im Vergleich zu einem Doppelmantel oder Halbrohrschlange zur Verfügung, da nur ein geringer Druckabfall über das Rohrbündel auftritt.
Die Reemaillierung und das Verwenden von PowerBaffles anstelle konventioneller Stromstörer schonen nicht nur Ihren Geldbeutel, sondern auch unsere Umwelt.
Ein Blick in die Zukunft
Freuen Sie sich auf weitere Artikel in den folgenden Newslettern zu energetischen Themen, unter anderem:
- Der CO2-Footprint aufgrund der Betriebskosten eines Rührwerkapparates
- Die „optimale Rührerdrehzahl“ für einen maximalen Wärmeaustausch
- Heizen und Kühlen beschleunigen und dabei Energie sparen
Literaturverzeichnis
[1] E. Kommission, „Der europäische Grüne Deal,“ Amtsblatt der Europäischen Union, Brüssel, 12/2019.
[2] THALETEC GmbH, DIN Rührwerksapparate CE1600-40000l - Flyer K006, Thale: THALETEC GmbH, 2012.
[3] M. S. C. A. Jannik Schlemme, „Energiewende in der Industrie - Branchensteckbrief der Eisen- und Stahlindustrie,“ Navigant Energy Germany GmbH, 2020.
[4] Umweltbundesamt, „Bilanz 2019: CO2-Emissionen pro Kilowattstunde Stron sinken weiter,“ [Online]. Available: umweltbundesamt.de. [Zugriff am 10 2021].