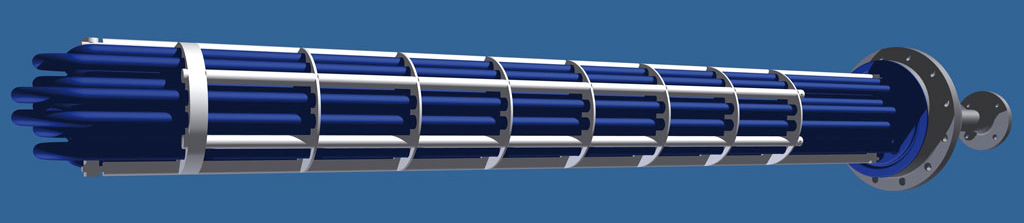
Glass-lined heat exchangers are used in process engineering operations where the following application criteria are essential:
- Optimum heat transfer with minimal loss
- Highest chemical resistance of the surfaces in contact with the product
- Graphite-free surface so that no unwanted particles are released into the medium, which may occur with graphite heat exchangers
- Smooth, easily cleanable surfaces
- Absolute impermeability of the entire system so that the plant can also be operated safely in a vacuum and at higher pressures (up to 16 bar)
- Potential for flexible and task-specific configuration
Accordingly, THALETEC heat exchangers can be used as condensers, evaporators or generally as liquid-to-liquid heat exchangers. All known liquid heating/cooling media can be used as media on the service side. Water, brine or thermal oil can be used without any problem.
With its heat exchangers THALETEC offers, inter alia, savings and optimisation potential in the area of process heat recovery, better utilisation of the energy and materials used as well as a reduction in unnecessarily high thermal resistance.
Gasket-free
The gasket-free glass-lined U-tube bundle heat exchangers from THALETEC have been tried and tested for over 10 years. The structural design and its manufacture are globally unique and protected by a number of patents.
The most significant and unique feature of THALETEC heat exchangers is the completely gasket-free connection of the glass-lined tubes with the similarly glass-lined tube sheet. As there is no sealing element, the application parameters of the heat exchangers are solely determined by the glass-lining. Limits which might arise from the resistance properties of renowned elastomer gaskets do not occur with the glass-lined heat exchangers from THALETEC.
The requirements of the GMP-compliant construction are thus safely met by the gasket-free connection system. Product residues and impact on the product are excluded by the basic concept.
If required, the tube/tube sheet connection can be released without causing damage so that individual tube sections can be replaced at any time.
Efficient and compact
To ensure optimum heat transfer during the manufacturing process of the U-tubes, a precisely defined layer thickness with a close tolerance is glass-lined with precision so that it is non-porous. The automated application process used for the glass-coating ensures a uniform material structure with extremely minimal variations in the thickness of the glass-coating. This guarantees even thermal distribution and counteracts thermal spikes in the glass-layer.
The entire structural design, together with the precision application of the glass-lining, gives a heat transfer coefficient of up to 800 W/m2K! Thus particularly compact heat exchangers are possible.
In accordance with the thermal design, THALETEC heat exchangers can be universally used for heating (e.g. as evaporators) or also for cooling (e.g. as condensers).
With regard to the length of the heat exchanger there are no limits in theory. The length of the tube bundle can be up to 4,500 mm, if required. The nominal diameter of the heat exchanger can be designed up to DN 600 in size.
In the diagram in Figure 3 reference values are shown for the heat exchange surface per metre of the tube bundle and the double wall depending on the nominal diameter of the heat exchanger. For example, the heat exchange surface of a heat exchanger with a tube bundle length of 1 metre and DN 300 nominal width is about 9 m2. A jacket around the casing of the heat exchanger provides an extra 0.9 m2of heat exchange surface. Accordingly, a heat exchanger with a jacketed casing and a bundle length of 4.5 m will give a thermally effective heat exchange surface of about 17.5 m2 (A=9.2 m2/m + 0.9 m2/m)*4.5 m = 44.45 m2). Simply put, a heat exchanger with the dimensions mentioned will have the heat transfer performance corresponding to a simple double wall heat exchanger with a surface of 44.5 m2. Further details can be found in Flyer K014.
In summary this means:
1 m2 of a heat exchanger tube surface has the same thermal transfer performance as 3 m2 of a simple jacket!
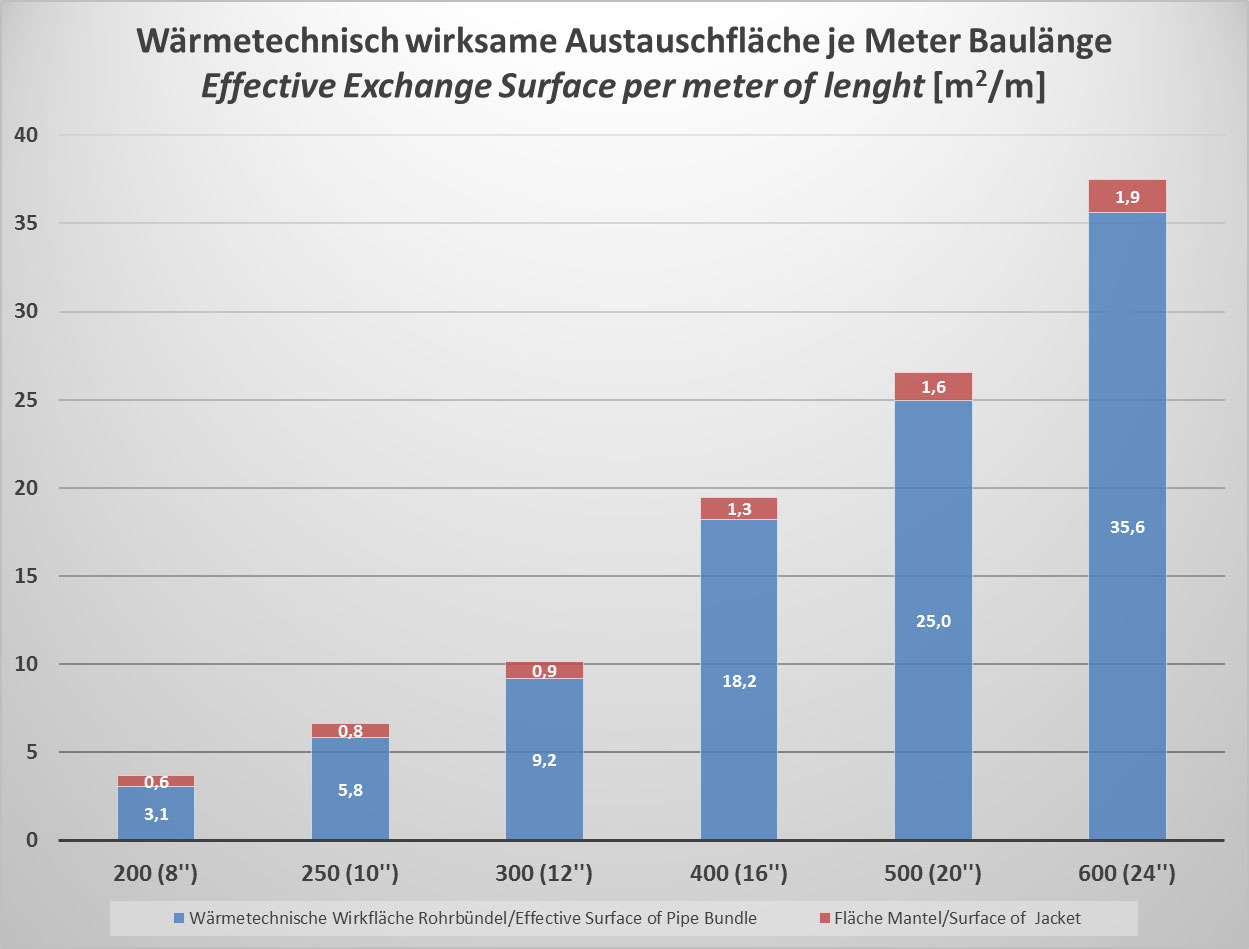
Figure 3: Thermally effective heat exchange surface per metre in length of the tube bundle depending on the nominal diameter
Comprehensive Standard
THALETEC heat exchangers are designed as standard for vacuum and pressures up to 6 bar on the product and service side. In special cases pressures on the product and service side can be achieved up to 16 bar. The maximum operating temperature is around 230°C and is restricted by PTFE components as well as the materials of the flange seals. The maximum permitted temperature difference between the product and the service medium is around 140 K. The design usually complies with the pressure equipment directive or the ASME code.
As standard, THALETEC heat exchangers are designed as single phase. In cases where the flow speed inside the tubes is insufficiently high, multiphase heat exchangers can also be implemented.
The video shows the assembly of a THALETEC heat exchanger in a glass-lined casing.
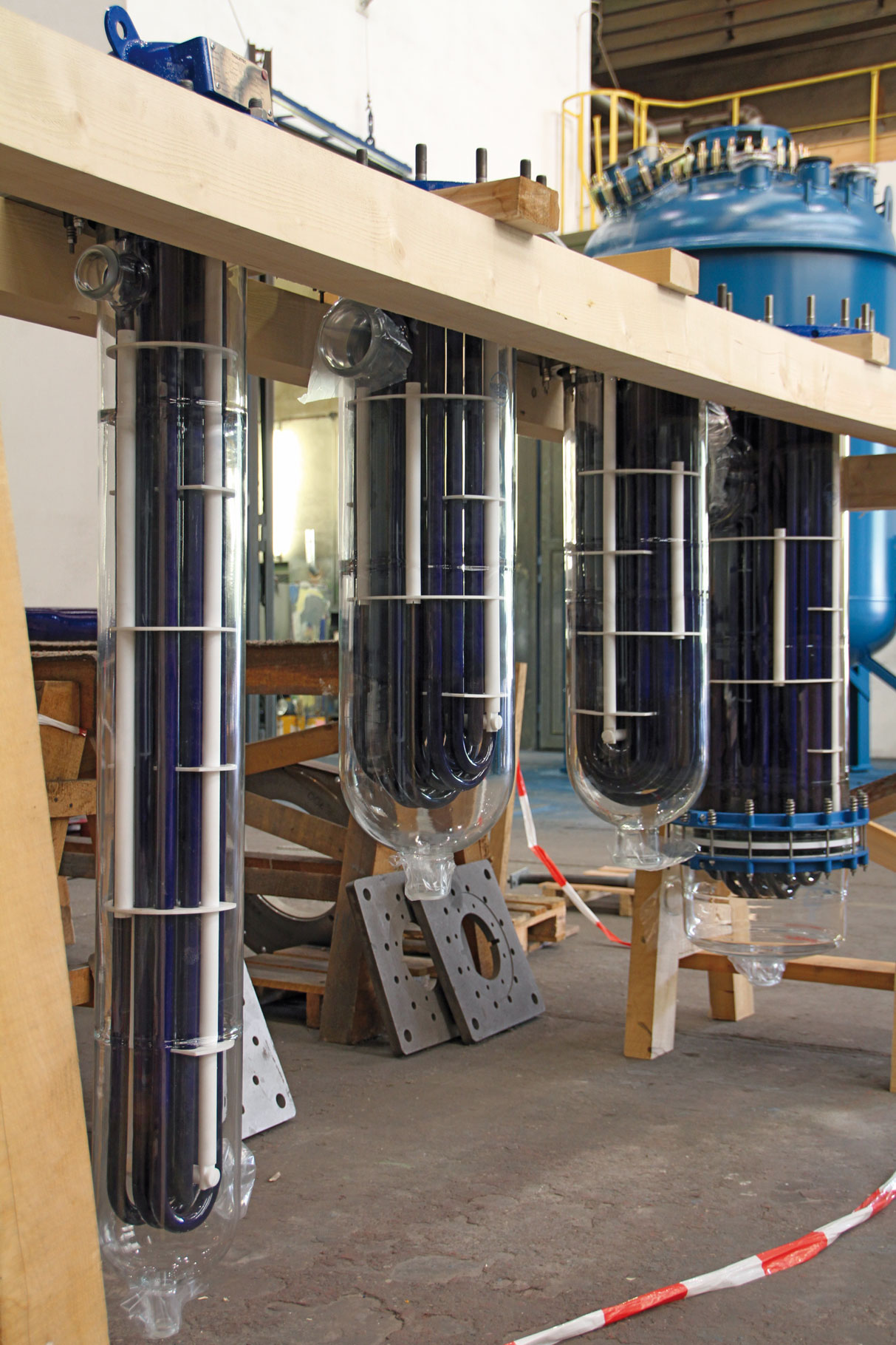
Figure 4: Assembly of THALETEC heat exchangers in production
Glass-lined heat exchangers from THALETEC are always individually tailored and structurally designed to the demands of the process. Fig. 5 for example, shows a heat exchanger fitted in a plant in a vertical arrangement. Besides the tube bundle the double wall also contributes to the thermal transfer.
Fig. 6 shows a heat exchanger used as a head condenser in a column. Using a loose flange connection the heat exchanger is set onto the head of the column, ensuring effective condensation of the accumulated medium
Fig. 7 shows a heat exchanger with a heat exchange surface of 21 m² in a vertical configuration. This is a design in accordance with the ASME code for an American customer. This construction is extremely suitable for integrating into existing plants. Heat exchange surfaces of this size can be realised in small construction volumes.
In Fig. 8 a heat exchanger is designed in a tandem arrangement. Two glass-lined tube bundles are installed in a casing and are operated respectively at a different temperature level. The tandem arrangement therefore facilitates the safe control of very high temperature differences between the heating and cooling medium and the product. There is no risk of damage as a result of thermal shock. However the structure of the heat exchanger is very compact and space-saving.
No contamination through interior-coated tubes
To prevent contamination and corrosion inside the heat exchanger tubes, THALETEC, together with a specialist, has developed a system to coat the inside of the heat exchanger tubes. The system is based on a stoved coating made of a thermosetting plastic material. The polymer base system is modified by special additives in such a way as to achieve perfect protection from incrustation and corrosion on the inside of the tube. In addition, the coating system is characterised by the following features:
- High thermal conductivity of the coating and impermeability with minimal coating thickness
- Sustainably high thermal conductivity
- Actively corrosion-resistant due to the hydrophobic surface
- Significant reduction in fouling occurrence due to the smoother and less adhesive surface; thus also significant reduction in cleaning outlay and increase in plant availability
- Minimized risk of electrostatic discharges
All-round programme
A comprehensive range of accessories completes the THALETEC heat exchanger programme. For example, the following accessories are available as an option:
- Glass-lined temperature measuring probe to measure the inlet and outlet temperature of the product (Fig. 9)
- Inspection glass-units to observe the processes in the heat exchanger
- Quick release cover for a visual inspection of the interior of the heat exchanger and for access for CIP cleaning.
Other components can be developed and supplied, as required.
Safe design
For the design and configuration of your optimum glass-lined heat exchanger our experts are at your disposal. In our brochure K014 you will find a questionnaire which will facilitate a full description of your specific requirements for your task.
Conclusions
THALETEC's glass-lined heat exchangers are safe and highly efficient apparatus which can be universally used in chemically demanding processes. In chemical applications as well as for those which require the highest product purity, glass-lined heat exchangers from THALETEC can outdo other materials with their positive characteristics. We would be delighted to help you conceive and manufacture the right and optimum design for your application. Just ask us! We would be pleased to assist you!