PowerBaffle makes a 30% increase in production possible
Experiences from the fungicide production
The problem
In an exothermic reaction to increase the yield, a higher heat release, which could not be achieved by conventional means, was required.
The process
In a continuous process involving an organic reaction mixture being hydrolysed with hydrochloric acid, a fungicide is produced in a glass-lined reactor at the premises of one of our customers. The process is highly exothermic and the removal of the exothermic heat is a determining process value for the yield.
Existing Installation
In the operation there is a glass-lined Type BE 2500 reactor from a foreign manufacturer. Hitherto, a release of the heat took place solely via the half-pipe coil fixed to the reactor.
No further possibility for heat removal was given with the existing equipment.
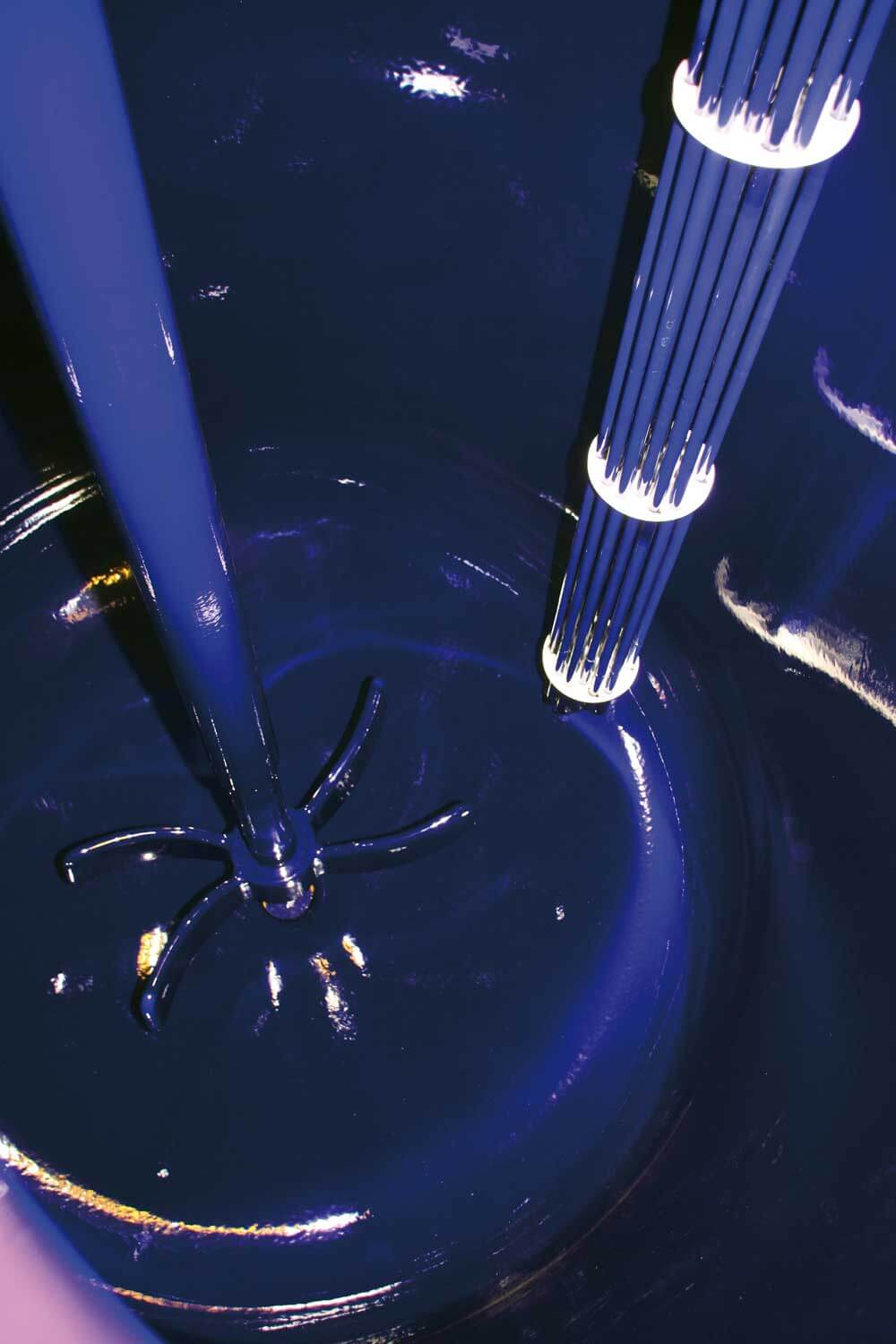
Figure 1: PowerBaffle incorporated into a 10m³ glass-lined reactor
External solutions for cooling
Until now, removal of exothermic heat was attempted via an external product cooling circuit.
In this case, the product stream was pumped by means of a pump through an external heat exchanger.
The high solids content of the product, however, led at very short intervals to the pump used being exposed to very heavy wear and repeated repair or even replacement due to cavitation and abrasion.
As this solution was associated with high maintenance costs, alternative solutions had to be sought. The aim here was to remove the exothermic heat within the reactor without having to replace the existing reactor.
PowerBaffle – Integrated solution for the safe release of heat in glass-lined equipment
After a thermo-technical consideration of the matter with the customer and a thermal design by THALETEC, it was decided to use a PowerBaffle.
With a PowerBaffle we have an effective and safe glass-lined heat exchanger which is incorporated in the glass-lined reactor and at the same time assumes the function of the baffle.
The PowerBaffle is inserted into the baffle nozzle instead of a conventional baffle and screwed to the loose flange. No special nozzles are required.
In the application described, a DN200 x 1,880 mm PowerBaffle was used with an exchange area of 1.86 m².
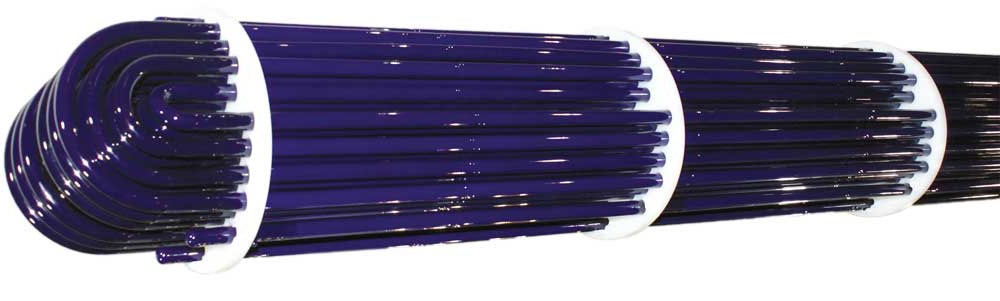
Figure 2: View of a PowerBaffle for a 20,000-litre glass-lined reactor with a length of 4400 mm
Increase in production capacity of 30%
Until now, heat was only released via the half-pipe coil, now the release of heat takes place via the half-pipe coil and the installed PowerBaffle.
Through the higher heat exchange, it was possible to increase the yield considerably.
The residence time of the product was reduced from 43 to 35 minutes and production capacity was boosted by 30% as a result.
Why is this increase achievable through a PowerBaffle?
With the glass-lined PowerBaffle, heat transfer coefficients of 800- 1.000 W/m² K can be reached.
If the heat transfer coefficients of a glass-lined reactor are compared with the u-value of the glass-lined PowerBaffle, a value results for the PowerBaffle which is up to three times higher than in the case of an reactor without such a system.
This means that one square metre of exchange area of the PowerBaffle corresponds to a comparable exchange area of three square metres of the wall of the reactor.
In this construct, the flow conditions and the media in the product space and in the pipes remain unconsidered.
By choosing a suitable agitating system adapted to the process, yet another improvement, often to the tune of a further 20-30%, can be achieved.
Amortisation and cost saving
The investment costs of the PowerBaffle had paid for themselves within one week.
Moreover, the cost of repairs for the pump which repeatedly had to be paid in order to repair and replace the external product cooling circuit is now saved.
Conversion period
The conversion of the existing system from „old baffle“ to the new glass-lined PowerBaffle took place within 3 days.
Time was mainly taken in dismantling the old, conventional baffle and installing the new integrated solution as well as adapting the piping in order to provide the PowerBaffle with coolant.
Experiences
The PowerBaffle is used by customers for many years without any problems in the production of fungicides.
Initial concerns about the glass-lining being exposed to heavy wear on account of the high turbulence between the glass-lined tubes and the solids in the product have not materialized.
In the meantime, a further process could be optimized by using another PowerBaffle on another existing apparatus.
Would you like more information?
If so, please send an e-mail to process@thaletec.com or kindly also contact a THALETEC representative in your area.