Optimum Flow Nozzles for all glass-lined apparatus with jacket – THALETEC AgiJet 50
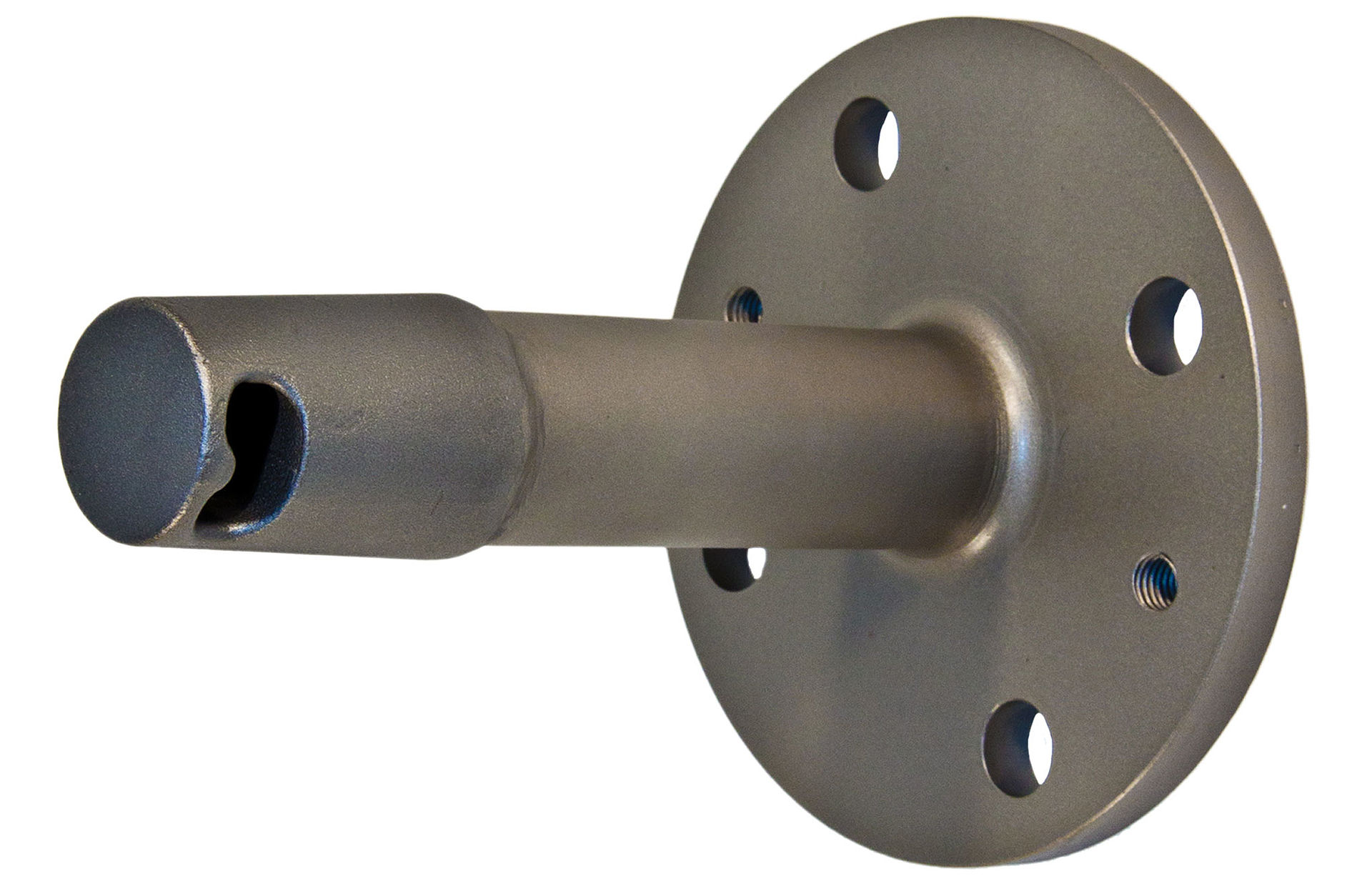
Basic designs of cooling and heating rooms
Glass-lined apparatus can be cooled and heated in various ways. Classically, they are equipped with a jacket or a half-pipe coil. Half-pipe coils offer a defined flow pattern and allow a high pressure level in the service room. The disadvantages are high costs, a smaller heat exchange surface and the risk of thermal stress cracks in the bottom dish under high thermal loads. Furthermore, a half-pipe coil causes a high pressure drop when pumping the service medium and therefore higher operating costs. The jacket, which can be operated with steam (without a flow nozzle) as well as with liquid service media, has the opposite aspects. As a historical solution for generating a tangential flow in the jacket, spiral baffles were welded onto the inside of the jacket. However, this variant is cost-intensive and corrosion damage leads to the failure of the spirals inside the jacket after a certain period of operation. At the same time, heat transfer is poor. Due to the relatively large tolerances of a glass-lined equipment, gaps also occur between the spirals and the inner vessel, leading to bypass flows and thus impairing efficiency (short-links between the jacket inlet and outlet). Flow nozzles for operating a jacket are a modern, efficient and cost-effective solution.
The limiting factor for the available heat exchange surface is the size of the apparatus. With the THALETEC PowerBaffle (K018), this limit is exceeded! The PowerBaffle combines the functions of a baffle, a temperature measuring system and a heat exchanger. Heat exchange surfaces can be effectively increased and process times drastically reduced! Another unique selling point is the THALETEC PowerCoil (K174), which is an improved half-pipe coil. This offers a larger heat transfer surface, lower pressure drops and greater safety thanks to improved weld seam quality.
Design and function of a flow nozzle
Flow nozzles are used to generate a tangential flow and thus an effective heat transfer over the entire vessel surface in the jacket. Flow nozzles are inserts for the jacket nozzle that have a flange at the inlet and a narrowing of the flow cross-section at the outlet. This narrow outlet is arranged at a 90° angle to the inlet and generates a high outlet velocity as well as a tangential flow pattern in the jacket. Flow nozzles can be used for all liquid operating media.
Figure 1 is based on a CFD simulation (K164) and clearly shows the difference between a jacket with and without a flow nozzle during operation. Without a flow nozzle, there are direct short-link flows between the jacket inlet and outlet. Significantly lower flow velocities can be observed at the same volume flow rate. The result is a very poor heat transfer, as only a small part of the service medium is exchanged in the jacket and only very low flow velocities prevail in the "active areas". The available heat transfer surface of a glass-lined apparatus is not utilised efficiently
THALETEC AgiJet 50 and AgiJetflex (K062)
Nominal sizes, layout and number of jacket nozzles are standardised for glass-lined reactors in DIN 28151. THALETEC offers AgiJet 50 flow nozzles (cover picture) to match. These are only available in the nominal diameter DN50 - suitable for all glass-lined apparatus. The nozzle outlet made of high-quality cast steel is highly wear-resistant and has a high outlet velocity (Figure 2), thus generating a high flow velocity in the jacket (i.e. high heat transfer!). An optimised geometry ensures low pressure drops and a minimal risk of cavitation. Thanks to the nominal diameter used, the AgiJet50 flow nozzle is suitable for all glass-lined appliances - including those from other manufacturers.
The AgiJetflex also offers the option of adjusting the axial length of the flow nozzle (Figure 3). This combines all the advantages mentioned above plus a simple length adjustment via a threaded connection. Adaptability to the length of the jacket nozzle is possible so that all existing devices can be easily retrofitted.
Summary
The AgiJet 50 flow nozzle from THALETEC can be used universally to operate a glass-lined apparatus with a jacket efficiently and cost-effectively. This combines high wear resistance with a high outlet velocity. A high heat transfer coefficient is realised over the entire heat exchange surface of the jacket. Do you have any further questions about heat transfer and energy-efficient operation of your glass-lined apparatus? Simply contact us at process@thaletec.com