ELIMINATING THE FEAR OF DAMAGE – REPAIRING GLASS WITH GLASS
Glass-lined equipment forms the "heart" of the plant in numerous process engineering procedures and thus determines availability and productivity.
Because of the high level of resistance to chemical corrosion and wear, as well as the smooth, easily cleaned and chemically inert surface, glass-lined equipment is often the first choice.
If glass-lined equipment is damaged, whether as a result of process conditions, mishandling or during maintenance or inspection work, a fast and reliable repair of the glass lining is essential.
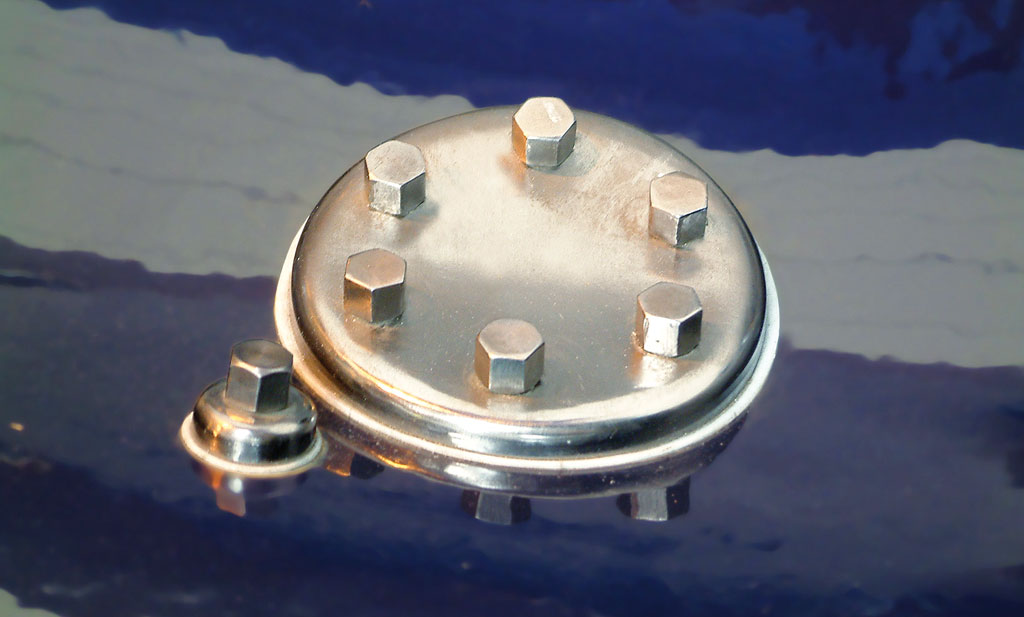
Repair site with tantalum covering elements
Accordingly, tantalum is a very "soft" material with low stability under mechanical demands, such as screw fittings or for parts requiring seal compression. Ultimately, the coefficient of thermal expansion of tantalum is only half that of steel.
For these reasons it has been extremely difficult, complex and expensive to date to conduct large-scale repairs to glass-lined vessels using covering elements made of tantalum.
Tantalum repairs improved
To date repairs have been based on protecting the damaged areas of the glass-lined surfaces in contact with the product from further corrosive attack using tantalum covering elements.
Tantalum screws, domed discs, tantalum plates and tantalum aprons are used depending on the extent of the damage. The covering elements are fastened to the damaged glass-lined component using screws and/or nuts made of tantalum.
The seal between the tantalum covering element and the glass-lined component is achieved using a PTFE sealing element.
In terms of the area of application tantalum is the only metal material comparable to the glass lining, the use of which, however, is associated with considerable disadvantages.
In particular, these are the material costs of the metal and the costs of the welding processes which must always be conducted in a controlled atmosphere.
In addition, tantalum becomes brittle with hydrogen, i.e. the broad range of the hydrogenation and dehydrogenation reactions can only be realised to an extremely limited degree in vessels repaired with tantalum components. Other metal materials, such as stainless steel or alloys, can only be used in severely restricted areas of application because their elements, especially Ni, Cr and Mo catalyse unwelcome secondary reactions. Whilst tantalum is a highly chemical resistant material, it does have extremely poor mechanical properties: its hardness is only in the range of 90-210 HV, its E-modulus is 186 GPa (steel 210 GPa), yield strength is 100-200 MPa and elongation is between 10 and 30%.
Glass-lined screw connections
THALETEC RepCaps (K091) are the component of choice when fitting corrosion-resistant screw connections inside glass-lined vessels. The RepCaps for which a patent application has also been made, comprise a special screw M8 made of the stainless steel A2 approved for pressure equipment, a sealing element made of multi-directional expanded PTFE as well as a glass-lined cap nut. The design of the special screw corresponds to that of a cylinder head screw according to ISO 4762 (DIN 912), but with an additional thread on the screw head. In order to create a screw connection, the component to be attached is firstly fixed with the special screw M8. Here torque of up to 12 Nm is possible, for tantalum screws only a torque of 1 to 2 Nm is permitted.
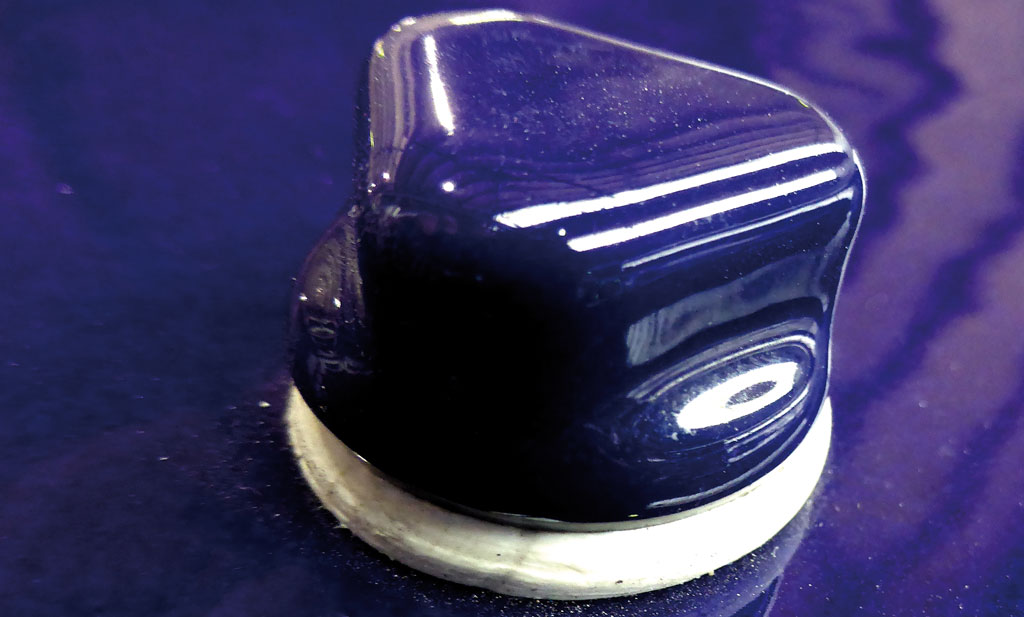
THALETEC RepCap
Then the glass-lined cap nut is screwed onto the head screw with the additional thread using a special key.
A sealing element made of FDA approved multidirectional expanded PTFE (Flyer K088) provides the seal between the cap nut and the component to be attached. The advantage of this connection method is obvious and lies in separating the functions of "fixing" and "corrosion protection": The pre-tension force of the connection is defined by the properties of the special screw which ensures the greatest mounting strength. Protection against corrosion for the screw connections is ensured, however, by the cap nut coated in the highly wear-resistant THALETEC ABRISIST (Flyer K028).
In addition, only glass-lined surfaces come into contact with the medium in the glass-lined vessel.
The THALETEC RepCap is the first high performance connection element with surfaces in contact with the product and which exclusively has an enamel coating, free from tantalum or any other metallic material.
RepCaps can also be used to attach glass-lined covering elements. The equally new THALETEC RepairPads (Flyer K094) are glass-lined circular discs which have one or more drilled holes. The discs are available in a concave and convex form with a diameter up to 100 mm. The surfaces of the RepairPads are coated with the chemically highly resistant and particularly wear-resistant THALETEC ABRISIST (Flyer K028). For repairs to surfaces which are accessible from outside, a special version is also available in which the covering element can be securely connected from outside.
Modern 3D scanning techniques for individual repair elements
RepairPads are used primarily to repair damage to the bottom of the tank, the tank walls as well as fitted components, such as agitators and baffles.
For surfaces on glass-lined components which do not correspond to regular geometry and are correspondingly complex, THALETEC offers a further, innovative repair procedure (Flyer K092): Using a 3D scanner a THALETEC service engineer captures the geometry of the damaged component, for example, damage to the tank in the area from the tank floor to the tank nozzles.
The 3D scan captured in this way is entered into a CAD system. A specialist engineer then develops a precisely matching piece on the basis of the scanned geometry.
This is "3D printed" from an alloy which can be coated using "Selective Laser Melting", an additive manufacturing process and is then coated with wear-resistant THALETEC ABRISIST.
The purely digital "work flow" ensures high quality and an accurate fit of the parts as well as fast processing time and thus only short plant downtimes.
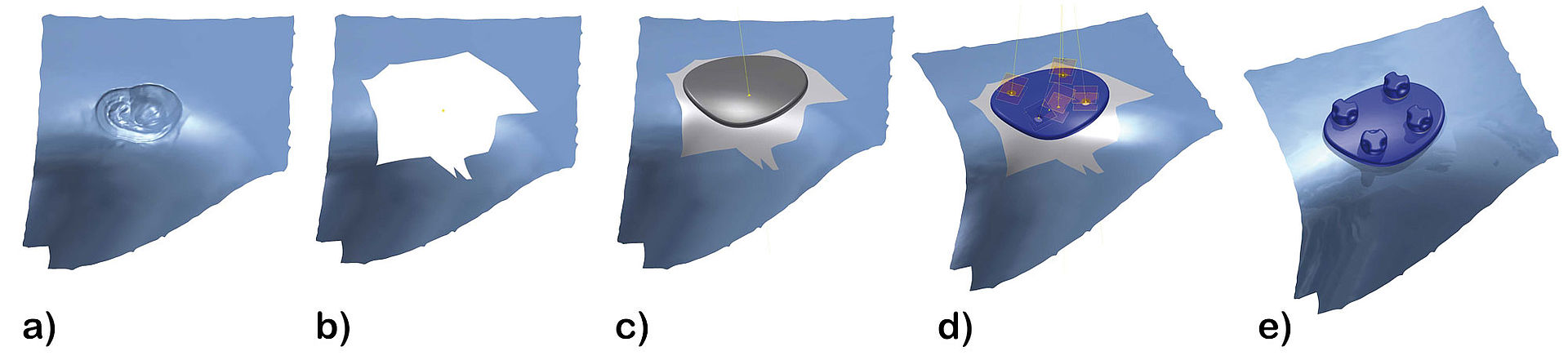
Construction of the glass-lined EmPad on the basis of the scanned 3D geometry
Damage to nozzles
The following additional repair systems are available to repair or cover damage to flange surfaces of tank nozzles or for other extensive repairs:
- PTFE repair aprons (Flyer K096) for repairing sealing surfaces and nozzle necks of tank nozzles up to DN 400
- The THALETEC Multi-Schürze (multi-apron) (Flyer K042) for repairing damage to manhole openings from DN 500 with an additional protective function against chipping and knocks.
- Complete repair sets (THALETEC RepSet) (Flyer K095) made of glass-lined steel to cover damage to nozzles and connectors permanently and safely.