"Well baffled!" –
Baffle-Technology for glass-lined equipment
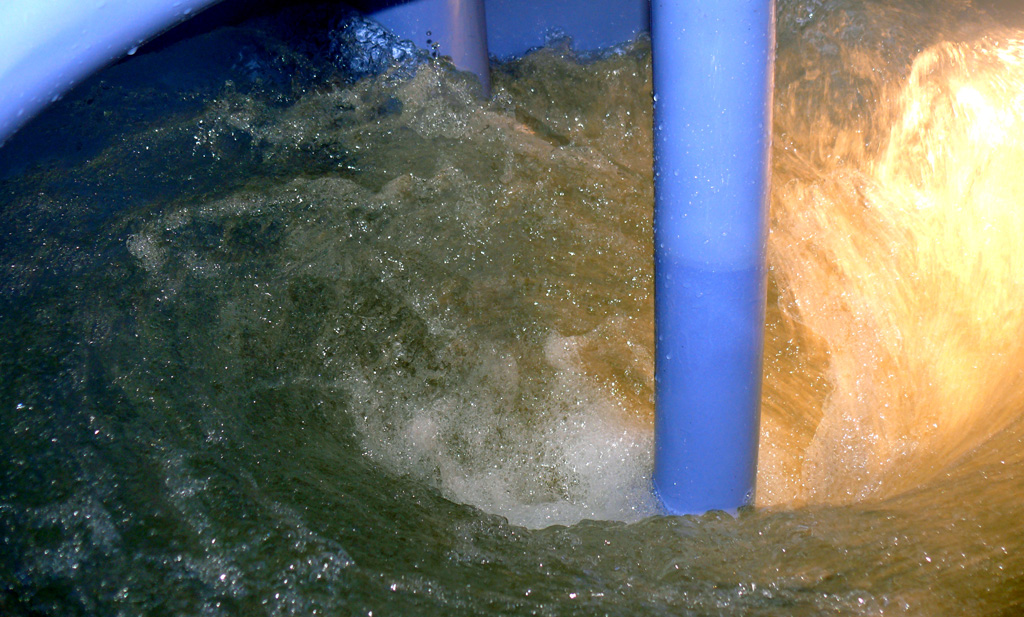
Flow influence of baffles
Baffles are an essential component of Mixing Technology and are often overshadowed by the topic of turbines. However, baffles can combine many functions and support specific processes. Only special cases with highly viscous products can be operated effectively without baffles. The majority of all processes are in the turbulent range and could only be operated inefficiently without baffles, resulting in long process times.
Without a baffle system, the product would perform a predominantly tangential movement in the vessel and mixing would only occur to a small extent. The main function of a baffle is to break this tangential motion, resulting in an axial/radial flow profile and mixing between all levels of the vessel. The disruptive effect and the turbulence created result in an increased power input and shorter mixing times.
The baffle effect of the baffle system in turn depends on the size, the design and the number of baffles. Often, one or two baffles are used in glass-lined apparatus in order to occupy/block as few nozzles as possible at the top dish. However, THALETEC offers various possibilities to introduce reactants via the baffle. Since turbines and baffles are exposed components in a reactor, they are subject to increased wear. A simple exchange in case of repair makes sense, which is not the case with wall-welded baffles, for example.
Types of Baffles (K165; S013)
THALETEC offers a wide portfolio of baffles to fulfil various tasks, to support specific processes and to integrate additional functions. A beavertail baffle is offered as a Standard Baffle (K020). This is standardised in DIN 28146, whereby THALETEC offers an extended version. This offers the advantage of a greater baffle effect. Moreover, smaller residuals can also be mixed effectively and even the temperature of it can be measured at the lower end of the baffle.
The DeltaBaffle (K057) was designed to achieve up to 15 % higher power input. The DeltaBaffle can be operated with a flat or pointed side in the direction of flow. The flat side causes a greater baffle effect and the described higher power input. If the DeltaBaffle is operated with the pointed side in the direction of flow, this offers particles a low angle of attack, so that there is less wear. This offers advantages in processes with high solids loading and/or particles with high hardness.
A MultiTube (K021) extends the functionality of the standard baffle by an internal dip pipe. The baffle can thus still be used to introduce substances that are to be introduced directly into the product and close to the turbine.
All the baffles mentioned so far can additionally be designed with a premium nozzle. This enables the introduction of substances via a inlet nozzle onto the liquid surface or into the gas space. This functional integration results in the PremiumBaffle (K020) and PremiumTube (K021).
If reactors are to be operated particularly efficiently from a thermal point of view, the use of a PowerBaffle (K018) is predestined. The glass-lined tube bundle combines the functions of a baffle, temperature sensor and heat exchanger. Due to the highly resistant thin-film glass-lining, particularly high-quality heat exchange surfaces are available. Process times can be drastically reduced and plant safety is increased. Separate cooling/heating circuits could be implemented and the operating costs are lower compared to a jacket and a half-pipe coil.
SEGTEC (K054) (Surface Effect Gassing Technology) is a simple and very efficient system for surface gassing and for sucking in floating solids. A significantly better distribution and retention time of the bubbles/particles are achieved in the reactor. Additional peripherals, such as pumps, filters or pipes are not required (Necessity for dip pipes and gassing valves).
The typically small sizes of the AE reactors only allow a limited number and size of nozzles on the top dish. In order to keep the few nozzles free for the operation of the chemical processes and at the same time to install an effective Mixing Technology, the RingBaffle (K167) can be used. This is integrated between the top dish and the lower vessel and carries the desired baffle design and number (Beavertail or DeltaBaffle).
THALETEC QuickTip – low-inertia and direct temperature measurement
THALETEC QuickTip (K061) is characterised by a very high measuring accuracy and a very good response behaviour with negligible inertia. The QuickTip temperature measuring system consists of a Flexsens 100 probe (K053) with 2x Pt100 elements and an electrically conductive glass-lined measuring tip. QuickTip temperature measuring systems can be integrated into glass-lined Standard Baffles, PremiumBaffle, MultiTube, PremiumTube and RingBaffle as well as into pure glass-lined temperature measuring probes. Within the scope of Reglassing, the QuickTip temperature measurement system can also be retrofitted to parts from other manufacturers. To increase redundancy, a QuickTip tandem (K114) can be used, which has two independent plug-in sensors with 2x Pt100 elements each in 4-wire circuitry.
Summary
In addition to the main task of baffling, baffles enable a wide range of additional functions. Depending on the process, various chemical reactions can be supported and enabled, so that process times are reduced. The THALETEC Baffle Selection Chart (K175) provides a selection guide for finding the right baffle. If you have any further questions, please do not hesitate to contact us at process@thaletec.com. We will be happy to help you select the right Mixing Technology!