Thermal package for glass-lined reactors
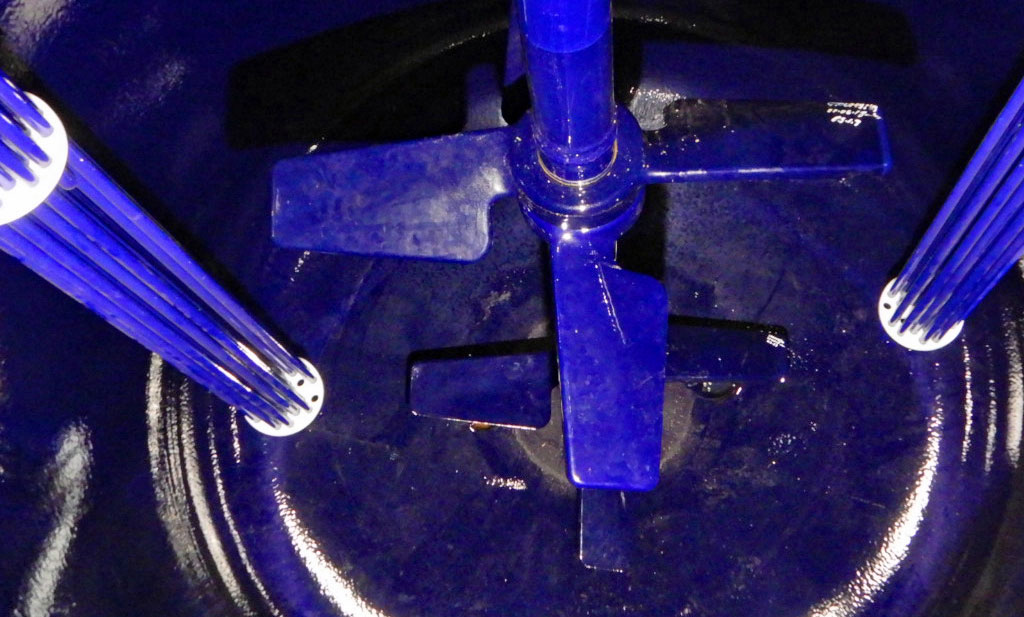
Introduction
Glass-lined reactors have to fulfil a large number of requirements in order to operate chemical reactions safely under aggressive conditions. These include, for instance, high corrosive resistance, very good cleanability, operation as a pressure device, avoidance of electrostatic charges, high productivity in a wide range of processes or adequate heat transport. The last point in particular is increasingly coming into focus, so that an energy-efficient operation is required. Rising energy prices as well as political guidelines and regulations justifiably encourage companies to assume an ecological responsibility. This article gives an overview of the options for heat transfer in glass-lined reactors and briefly summarises the advantages and disadvantages of the various options. The focus is on topics such as jacket vs. half-pipe coil, the insulation of a reactor, influencing variables on the heat transfer and the influence of additional heat exchange surface.
Jacket vs. Half-pipe coil
An often controversial topic is the use of a half-pipe coil or a jacket. Both variants have advantages and disadvantages under certain operating conditions. The following table gives a general overview of various aspects in a direct comparison.
Jacket
+
- entire heat exchange surface in use
- more cost-effective production
- lower pressure drop
- turbulent spiral flow through flow nozzles
- simple support structure of vessel
- good condensate discharge when using steam
- easy repair of the vessel in case of damage or breakthroughs
- reglassing possible up to 3 times without problems
- easy refurbishment of jacket (entire accessibility after dismantling of the jacket)
Half-pipe coil
+
- lower volume flow
- simple construction of several heating zones
- defined flow pattern
- pressure higher 6 bar can be easily implemented
- less piping effort
- reglassing possible up to 2 times without problems
- multi-circuit (parallel half-pipe coils; separation of service circuits)
-
- smaller heat exchange surface (especially with multi-circuits)
- more cost-intensive production
- higher pressure drop
- more complex support structure of vessel to avoid loss of heat exchange surface
- disruptive condensate discharge when using steam
- risky repair of the vessel in case of damage (condition of the weld seam)
- poor to no reconditioning of the interior of a half-pip coil (no access; on flushing)
- thermally induced stress cracks (especially at the bottom)
The comparison shows that a jacket has more advantages than a half-pipe coil. Nevertheless, the use of a half-pipe coil is justified if lower volume flows, several cooling/heating zones, separation between cooling and heating medium (multi-circuit) or higher steam pressures (> 6 bar) are required. Furthermore, the piping effort is usually lower.
Influencing variables on the heat transfer
Enamel is a poor heat conductor, so that its layer thickness has a great influence on the heat flow (Q) and limits it. This makes it all the more important to set the other parameters that influence the heat flow correctly. In general, glass-lined reactors are tempered via a jacket or a half-pipe coil. The heat exchange surface is thus predetermined and limited by the size of the reactor (A). The temperature difference (Δtm,log) between the product and the service medium has a significant influence on the resulting heat flow, but should be kept at a low temperature level to minimise heat losses to the environment.
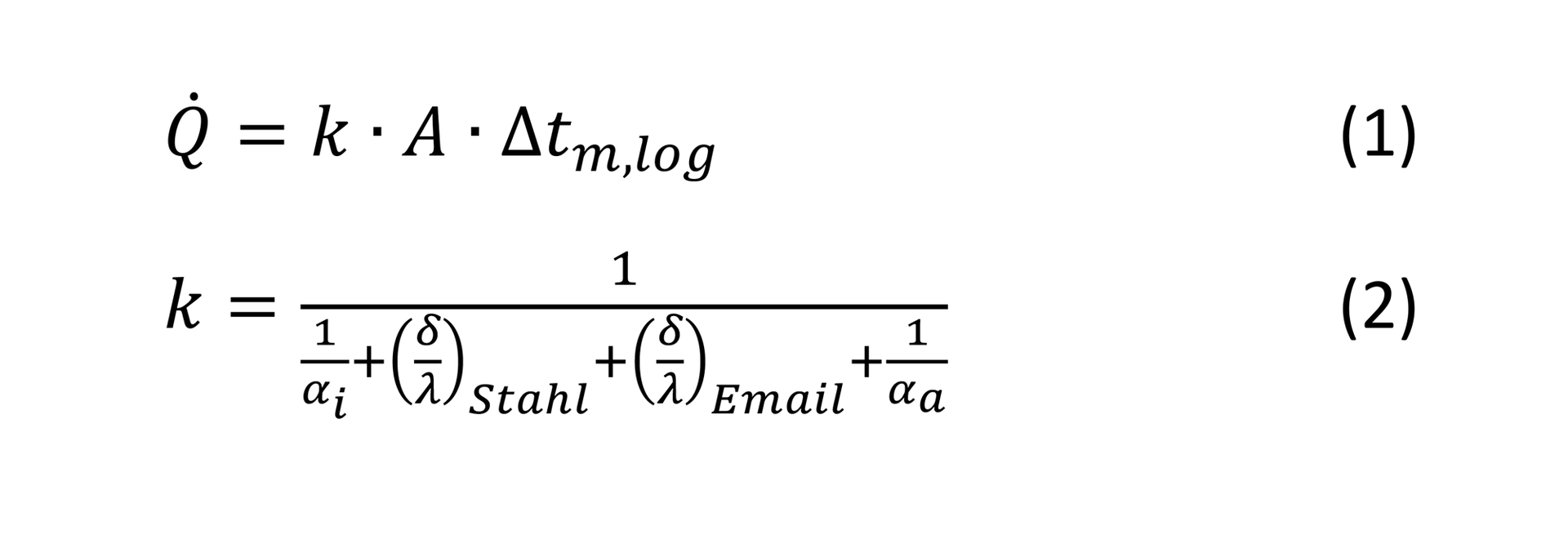
There are several possibilities for increasing the k-value under the given the heat conduction of the composite material (steel/enamel). The heat transfer (αa) between the outer wall of the inner vessel and the service space of the jacket/half-pipe coil is influenced by the material parameters of the service medium and the flow velocity. For generating a good heat transfer, the service medium should have the following material properties:
- High thermal conductivity
- Low viscosity
- High density
- High specific heat capacity
A high flow velocity, caused by the applied volume flow, also increases the heat transfer (αa). However, this influencing variable is limited and follows a root function and thus approaches a limit value (Figure 2). Consequently, an increase in volume flow increases the transmittable heat flow only slightly above a certain range and does not make sense anymore.
The heat transfer (αi) at the inner wall of the vessel and the product is also dependent on the material properties and the flow velocities. The material influencing variables are predetermined by the chemical process and cannot be changed. The flow velocity inside the vessel is determined by the type and number of turbines and the rotational speed. The configuration of the turbine(s) and the rotational speed are limited by the process (e.g. crystallisation, polymerisation). As well, the influence of the flow velocity again follows a root function and is thus limited. In addition, the mechanical power of the agitator induces a heat flow, which is counterproductive in a cooling process (Figure 3).
Insulation materials for glass-lined reactors
A reduction in heat loss to the environment and consequently an increase in energy efficiency can be achieved with an insulating jacket. This can cover the cylindrical part and the lower bottom or the complete reactor including the upper bottom, which takes more effort to insulate. Typical insulation materials are foam glass, mineral wool or rock wool. All materials are non-combustible and have different thermal conductivities. The insulation thickness depends on the material, whereby foam glass cannot be used to insulate the upper bottom. The jacket with tightly welded stainless steel sheets is essential to prevent corrosion of the reactor inside the insulation space.
The PowerBaffle – more power and shorter process times
The given heat exchange surface is predetermined and limited by the size of the reactor (jacket or half-pipe coil). If cooling or heating processes should proceed faster or with greater safety, the heat flow must be increased. A significant increase in heat flow can be achieved by enlarging the heat exchange surface. Glass-lined tube bundle heat exchangers - PowerBaffle K014 - represent a unique system for significantly increasing the heat exchange surface. This not only significantly increase the heat exchange surface and thus the heat flow, but also make it available at low operating costs due to its low pressure drop. Depending on the conditions, PowerBaffles have a k-value that is 2.5 to 3 times higher than that of a glass-lined vessel. Therefore, the surface of a PowerBaffle represents a particularly high-quality heat exchange surface! This is due to the glass-lining technique called “PUESTA” (powder electrostatic process). The same chemical resistance is achieved as with standard glass-linings (vessels, turbines, baffles) - however, a smaller layer thickness of the glass-lining is sufficient with PUESTA and thus the heat transfer is increased. One or more PowerBaffles can be connected in parallel or series to the jacket/half-pipe coil. The parallel connection could also be used to separate the heating and cooling circuits.
Summary
The mentioned aspects show that various limits and influencing variables must be taken into account with regard to heat transfer. It is also clear that increasing the heat exchange surface is the most ecological and economical way to increase the available heat flow. THALETEC is the only manufacturer in the world offering the PowerBaffle K014, which significantly increases the heat flow and at the same time acts as a baffle and temperature sensor. Just contact us if you have any questions about the heat technology of glass-lined reactors. THALETEC offers you the assessment and calculation of the various thermal aspects K164 process@thaletec.com.