55 % less CO2 through Reglassing at THALETEC
By Reglassing at THALETEC instead of building a new glass-lined reactor, more than half of the CO2 emissions can be avoided.
The chemical and pharmaceutical industries generally have a high energy consumption not only during the operation of their plants, but also during the production of necessary equipment, such as heat exchangers, agitators or wiped film evaporators. Enormous heat flows and drive power must be transferred as efficiently as possible and reused intelligently. The scarcity and rising cost of resources as well as the EU's "Green Deal" [1] and national regulations are encouraging companies to develop an energy-efficient infrastructure in order to assume social responsibility. The chemical and energy branches in particular represent a crucial sector due to their high energy consumption.
Glass-lined reactors – Heart of many chemical processes
Glass-lined reactors are a core element of the chemical and pharmaceutical industry and, due to the high steel input and the glass-lining process, have a high energy input during production. Due to the frequent production and the associated database, this is to be exemplified with the standardised reactor CE - 16000 - 2600 - AM (based on DIN 28136 3) with the help of the THALETEC-specific energy expenditure for the manufacturing process (Figure 1). This is compared with an identically constructed reglassed reactor.
A glass-lined CE 16000 reactor with jacket, fully equipped with agitator, stirrer and baffle, weighs about 17 tonnes [2]. About 10 tonnes are accounted for by the so-called "inner vessel", the glass-lined pressure vessel. The diameter of the reactor is 2700 mm, the length of the vessel 4080 mm. If the vessel stands on tube feet and has a drive, the total height is about 7100 mm. The reactor has a nominal capacity of 16000 l and a total volume of just over 18000 l.
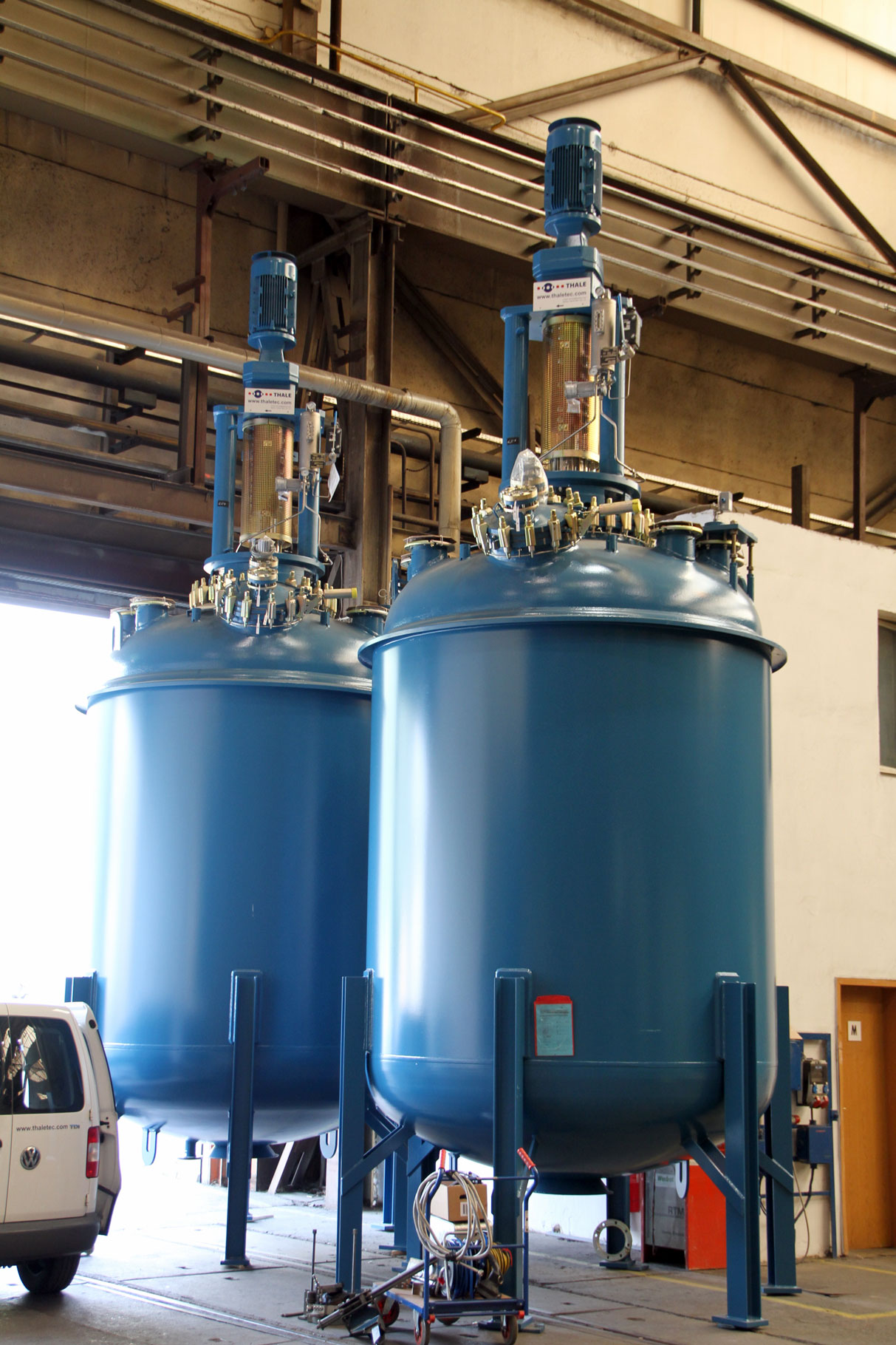
Figure 1: CE 16000 glass-lined reactor
Energetic aspects
The energy considerations take into account the aspects of steel production and in-plant manufacturing, including the glass-lining process. According to a study from 2020, the production of one tonne of steel requires approx. 3962 kWh [3]. This value includes both primary and secondary steel. The primary production from iron ore to the secondary steel from scrap is divided into approx. 70 to 30 % [3]. With a total mass of a CE16000 of approx. 17.95 t (incl. drive, agitator, baffle etc.), approx. 71100 kWh are required for steel production. In contrast, the steel is reused in the case of reglassing. In-house calculations show that the energy required for the shell work and other production steps of a new production requires approx. 4000 kWh and for reglassing approx. 2200 kWh.
Besides steel production, the glass-lining process is the second energy-intensive manufacturing process for producing a glass-lined reactor. The energy input for glass-lining a newly manufactured reactor and a reglassed reactor is equivalent at around 56200 kWh. Figure 2 shows the energy shares for the production of a reactor graphically.
Reuse of the steel body saves CO2
In total, a new production of the CE16000 requires an energy input of about 131300 kWh. In comparison a reglassing requires around 58400 kWh. This corresponds to an energy saving of -55 %. This is mainly due to the saving of energy for steel production.
This significant difference is also reflected in the CO2-footprint. Assuming the German electricity mix in 2019 (0.408 kg/kWh CO2) [4], around 53.6 t of carbon dioxide are emitted for the production of a new CE16000 and around 23.8 t for reglassed one (Figure 3).
Taking social responsibility
THALETEC GmbH takes its social responsibility seriously and identifies a high potential for saving greenhouse gases by using renewable energy.
As the furnaces are electrically operated, production including the glass-lining process would be possible with almost no emissions by using 100 % of renewable energy.
Even more CO2 savings possible through more efficient operation
The available and conservative results also show that it is not only more economical but also more ecological to operate one efficient reactor (instead of several and inefficient ones), which allows high heat flows and thus short heating and cooling times as well as high productivity.
Due to physical circumstances, the heat transfer is lower with glass-lined reactors because of the heat conduction properties of the glass-lining. A significant increase in heat flow can be achieved by enlarging the heat exchange surface with a PowerBaffle, which can be adapted to any standard nozzle DN 200 to DN 400 (Figure 4). This also provides the heating or cooling capacity at lower operating costs compared to a jacket or half-pipe coil, as only a small pressure drop occurs across the tube bundle.
Reglassing and using PowerBaffles instead of conventional baffles not only saves money, but also protect our environment.
Preview
Look forward to more articles in the following newsletters on energy-related topics, including:
- The CO2 footprint due to the operating costs of a stirrer apparatus
- The "optimal agitator speed" for maximum heat exchange
- Accelerating heating and cooling while saving energy
References
[1] E. Kommission, „Der europäische Grüne Deal,“ Amtsblatt der Europäischen Union, Brüssel, 12/2019.
[2] THALETEC GmbH, DIN Rührwerksapparate CE1600-40000l - Flyer K006, Thale: THALETEC GmbH, 2012.
[3] M. S. C. A. Jannik Schlemme, „Energiewende in der Industrie - Branchensteckbrief der Eisen- und Stahlindustrie,“ Navigant Energy Germany GmbH, 2020.
[4] Umweltbundesamt, „Bilanz 2019: CO2-Emissionen pro Kilowattstunde Stron sinken weiter,“ [Online]. Available: umweltbundesamt.de. [Zugriff am 10 2021].