Introduction
Time and again the question comes up in practice as to the point at which liquids should be dispensed in an agitated vessel in order to achieve the homogeneous distribution of the supplied medium as quickly as possible. The question also comes up time and again – regardless of the agitator used – as to what influence the baffle has on the mixing time, i.e. the time needed to achieve a homogeneous distribution of the supplied medium. For the required statements to be able to be made, extensive studies were conducted on a model THALETEC agitation system at Anhalt University of Applied Sciences in Köthen.
The following were investigated:
- How is the mixing time affected by the choice of the inflow point (when the liquid in the reactor is introduced onto the surface)?
- Which baffle system gives the shortest mixing time? In this connection, the paddle baffle and Delta-Baffle (pointed and blunt flow) types of baffle were examined
- Which baffle system results in the lowest amount of specific mixing work?
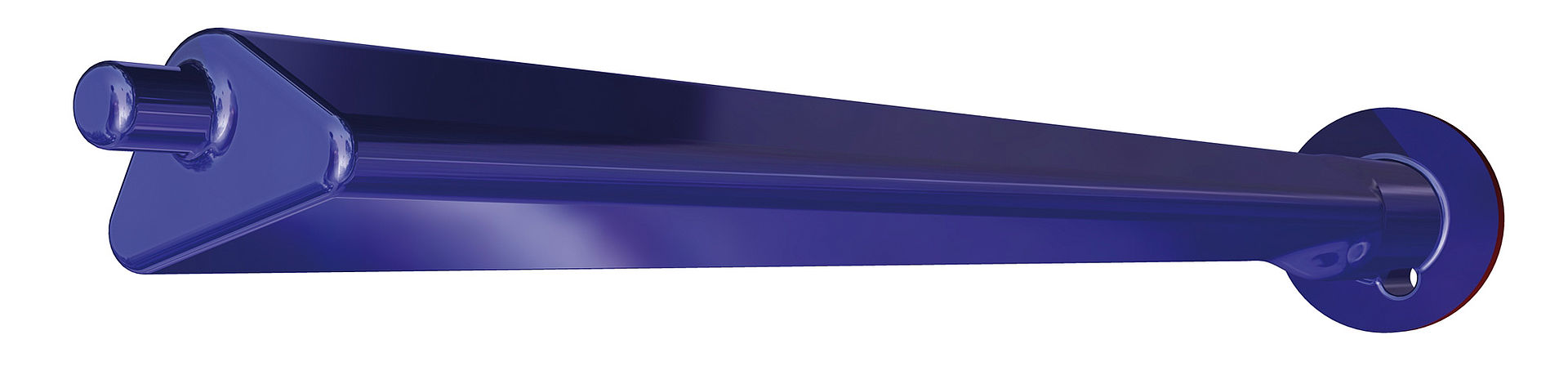
The optimum feeding point
According to Figure 2, the feeding points were set as follows:
- Just in front of the baffle
- Immediately behind the baffle
- 180° relative to the baffle, at half tank radius (midway between the agitator shaft and tank wall)
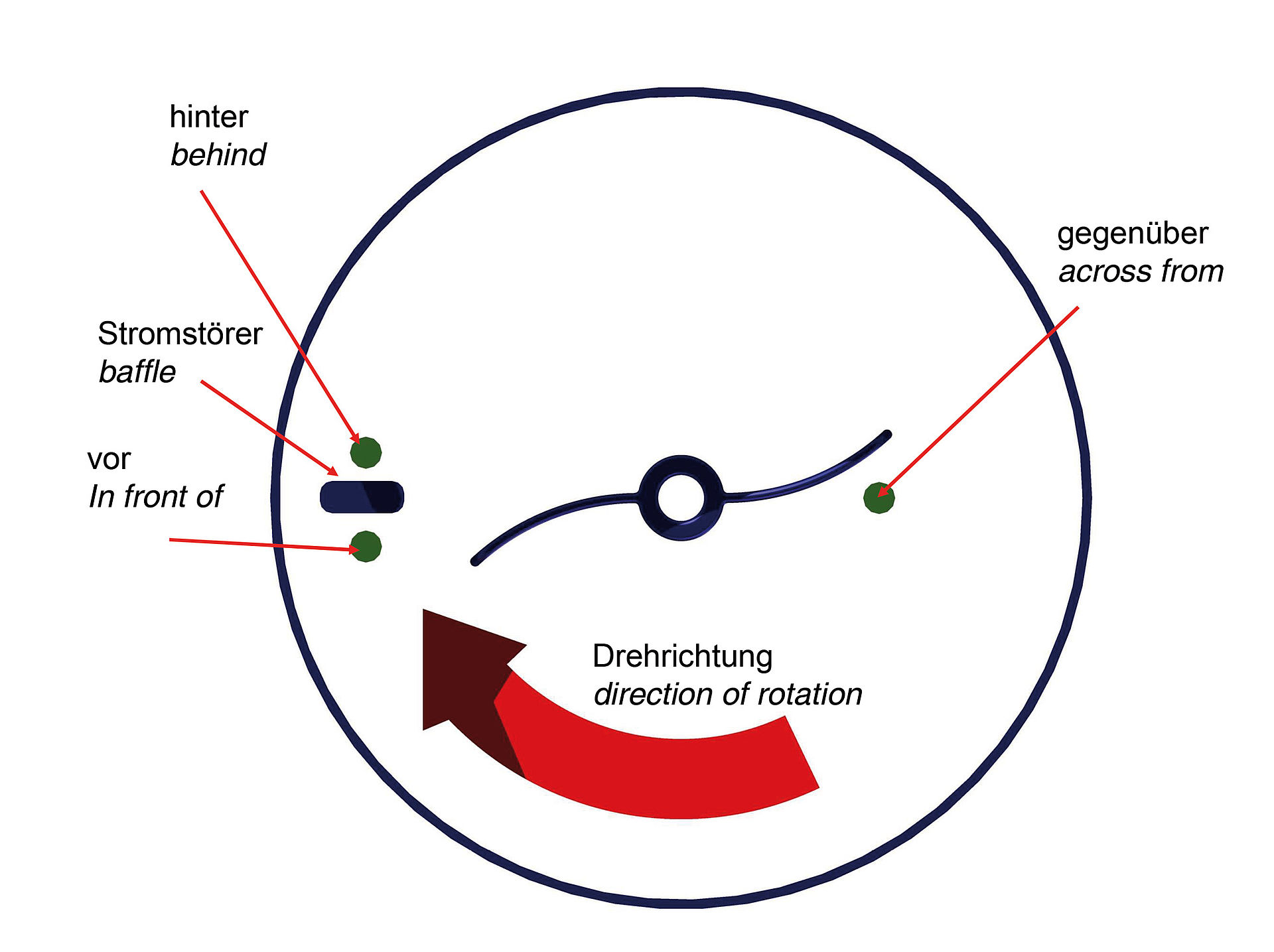
Figure 2: Feeding points: in front of, behind and across from the baffle. Direction of rotation of the agitating element clockwise.
THALETEC RCI in use
As an agitator, a single-stage THALETEC RCI eco was used. The baffle configurations tested are set out in Table 1:
Mixing time dependent on the feeding point and the baffle system
As can be seen in Figure 3, there is each time a difference in mixing time depending on the feeding point (in front of, behind or across from the baffle) until a homogeneous mixture is achieved. The greatest differences in mixing time arise, depending on the baffle used, where the medium to be mixed in is in front of the baffle. If instead of a paddle baffle a Delta-Baffle with blunted flow is used here, the mixing time in this configuration can be reduced by almost 40%!
The mixing time in the different baffle systems does also vary, although not so evidently, in the case of the other feeding points investigated: In all cases, however, it is evident that the Delta-Baffle with blunted flow allows the shortest mixing time.
The ideal feeding point by using the optimum baffle configuration (Delta-Baffle) is obviously that in front and with some reservations, that behind the baffle, according to the investigations carried out.
THALETEC Delta-Baffles have an additional nozzle on the baffle flange, which allows this optimum inflow point to be reached easily, without a further reactor nozzle having to be allocated for the purpose. The introduction of liquids via this so-called ‘premium nozzle’ also avoids the spraying of the liquid.
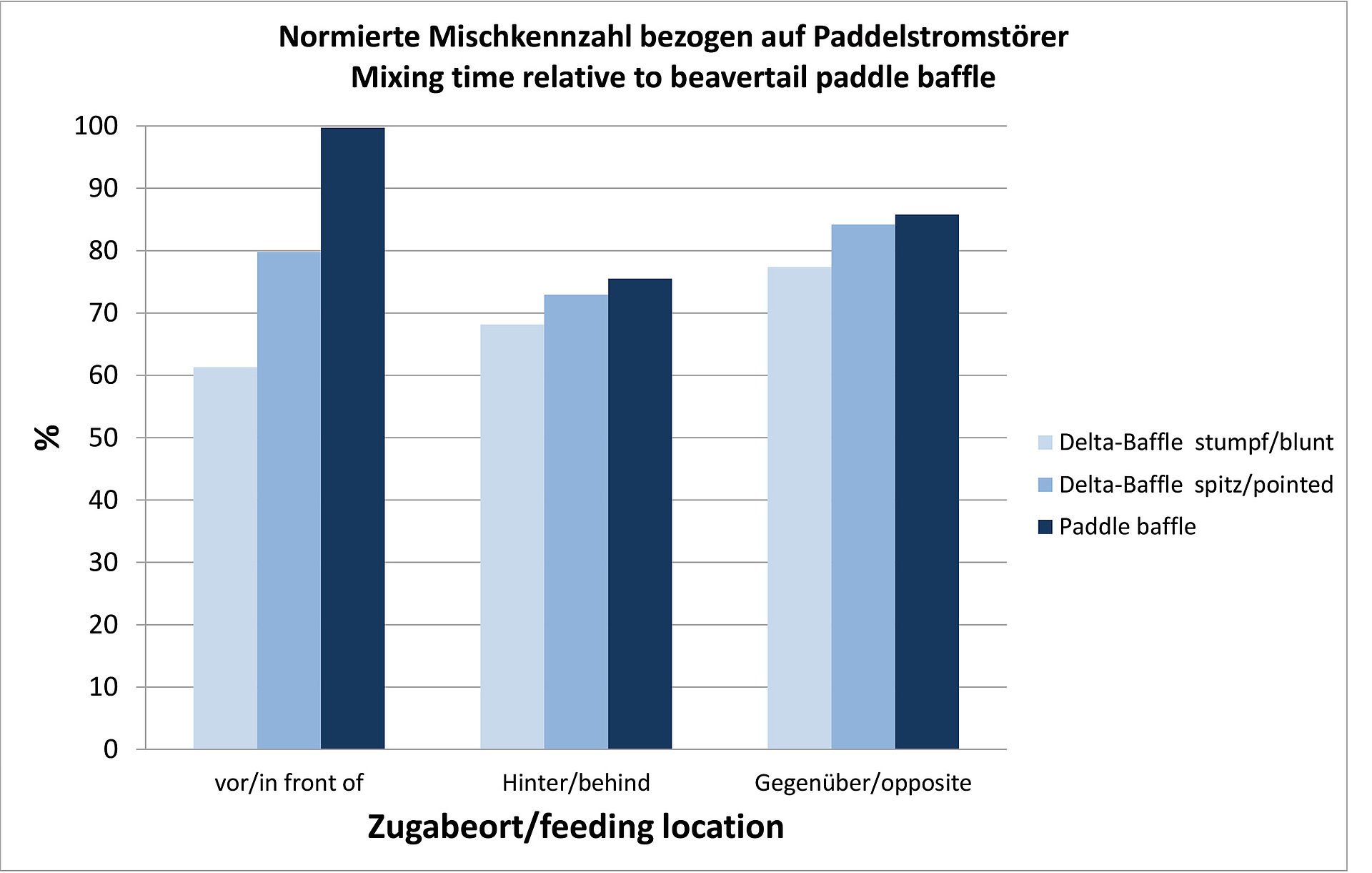
Efficient introduction with the lowest amount of specific mixing work
The specific mixing work is that related to the filling volume of the reactor (in Joules/m3) which is required to achieve a homogeneous distribution of the injected medium in the reactor content. The less specific mixing work there is, the more energy-efficient, and therefore more economical, the mixing process is.
The most energy-efficient baffle
Figure 5 shows the specific mixing work with a blunt flow Delta-Baffle and a paddle baffle, in both cases with the addition of the medium directly in front of the baffle, dependent on the Reynolds number (Re). The great difference in the specific mixing work of the two compared configurations can clearly be seen.
With a mean Reynolds number of 8.5 + 105, there is a specific mixing effort of about 800 Ws/m3 in the case of the blunt flow Delta-Baffle, where as the specific mixing effort in the case of the paddle baffle is about 1,600 Ws/m3, which is thus almost twice as high! On that basis, half of the energy can be saved when homogenising with the Delta-Baffle compared with the paddle baffle which is still in widespread use today!
Using the best baffle technology currently available, namely the THALETEC Delta-Baffle, the specific mixing work can be influenced by the choice of the feeding point.
The lowest specific mixing work is therefore achieved when the medium to be introduced is added in front of the baffle.
Compared with the addition across from the baffle, there is an improvement here of some 30% (where Re = 8.5 × 105).